Carrying on from my latest design a bike for me thread, I’ve started building the frame. I have decided to go for 29er wheels (and not bothering with 27.5+), and similarish geometry to the fargo, although I will be steepening the head angle a little bit (0.5-0.75deg), while shortening the stays a by about 8mm.
As some of you may remember, I have been keeping the insulation tape industry alive with some of my past frames, so for this build I decided to splash out and get some (marginally) better equipment. Those that know their Tupperware catalog, will spot that what I’m using as the catch pot and pump is a Vacuvin coffee storage container, which can easily reach 27inHg of vacuum, so perfectly adequate for resin infusion.
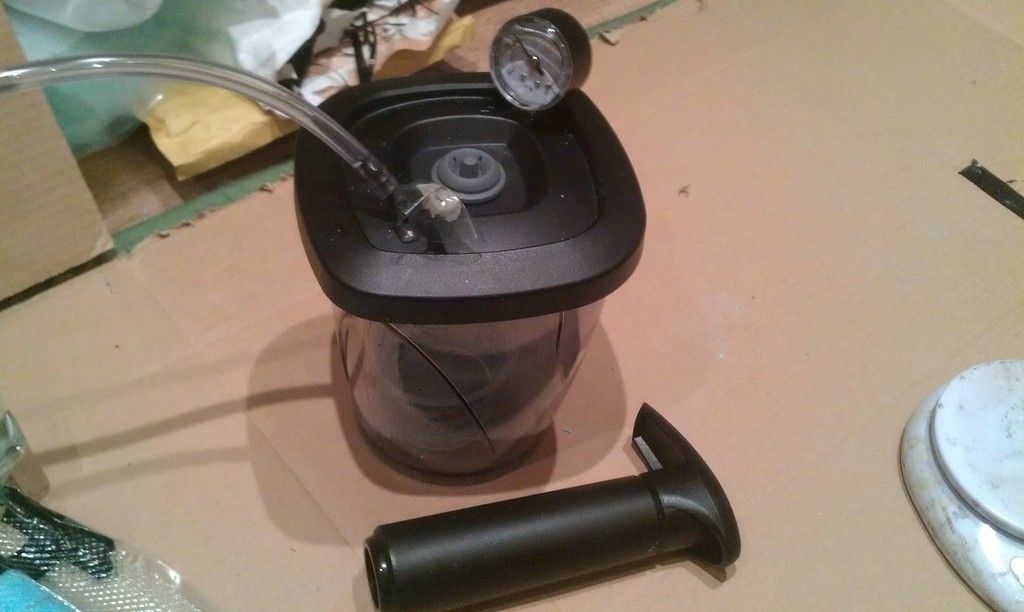
I have tarted the CAD up a bit to help visualize how it will all look together (I wont be running a -17 degree stem, that was just to see what my range of adjustment would be). By my calculations a -6deg 90mm stem should be about right and is what I have in the spares box.
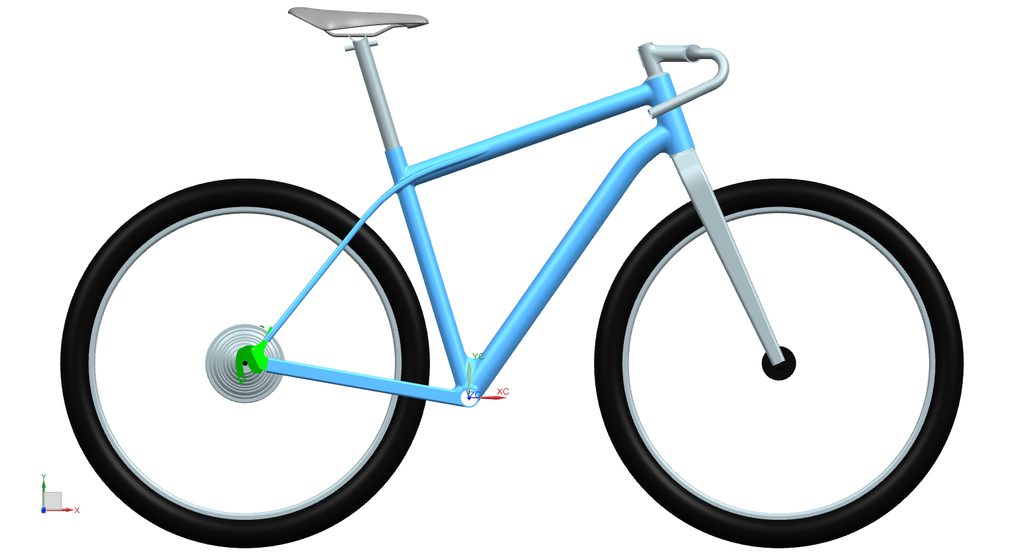
I’ve had some dropouts cut (about 5 sets it total; 3 geared, 2 ss) so all my future builds should be able to be interchangeable (No I will not be going boost 148)
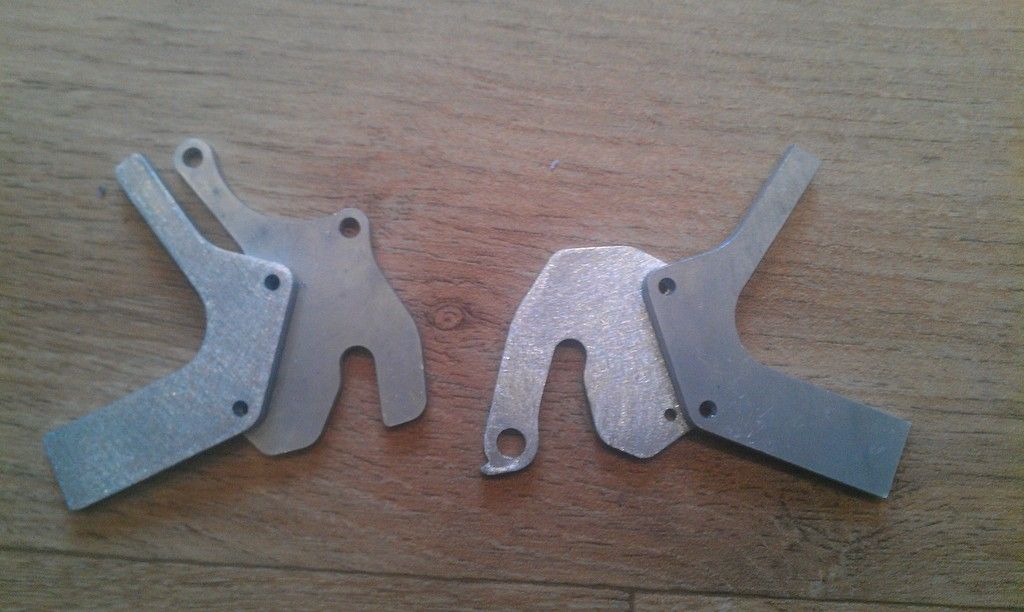
For the smaller tubes (seat and chainstays) I’m first fibreglassing them to increase their rigidity before cutting the centers out, as I had problems with the past 2 frames of the foam cores snapping.
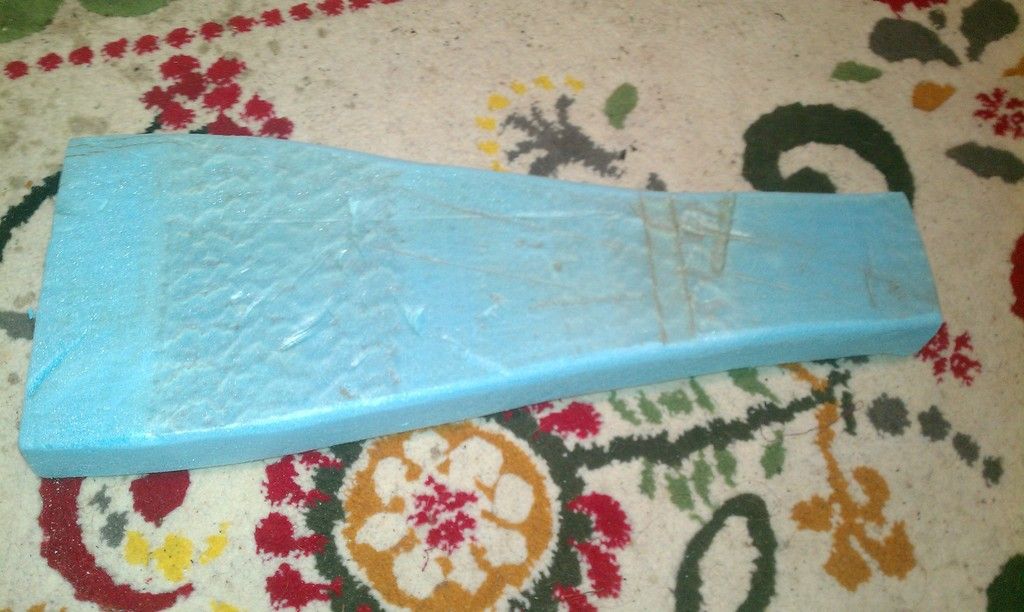
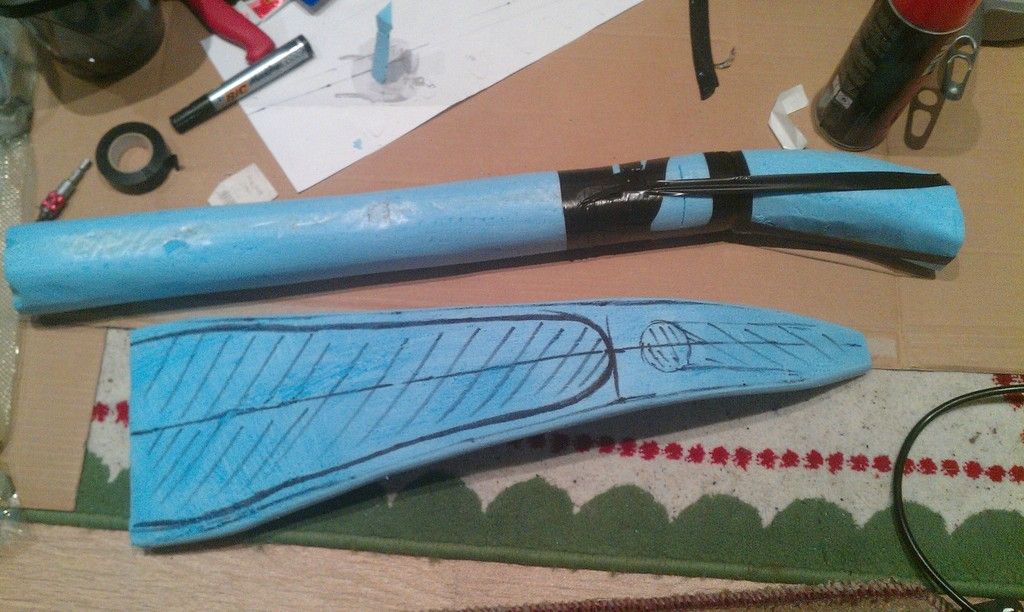
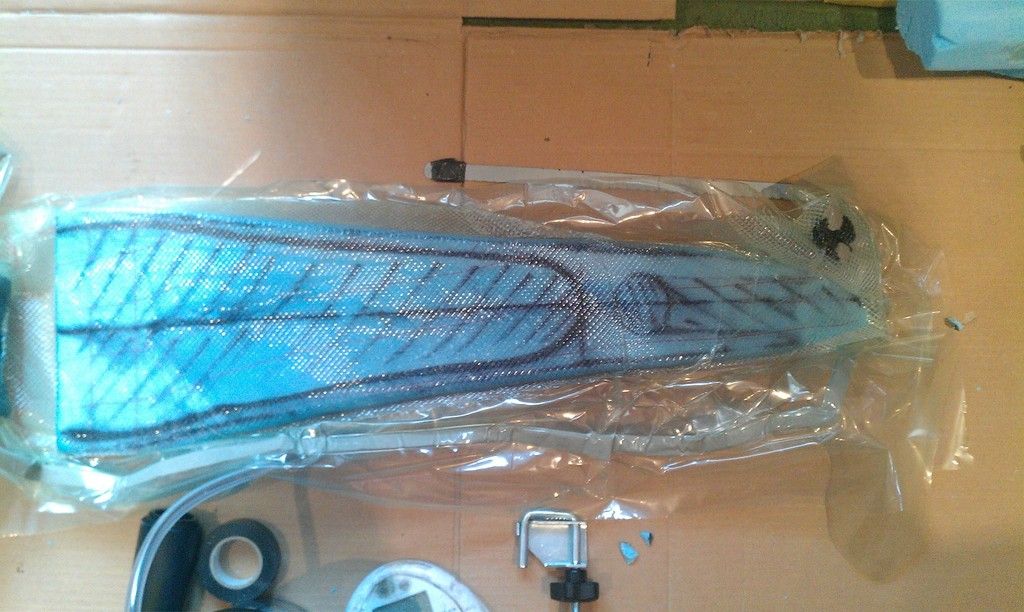
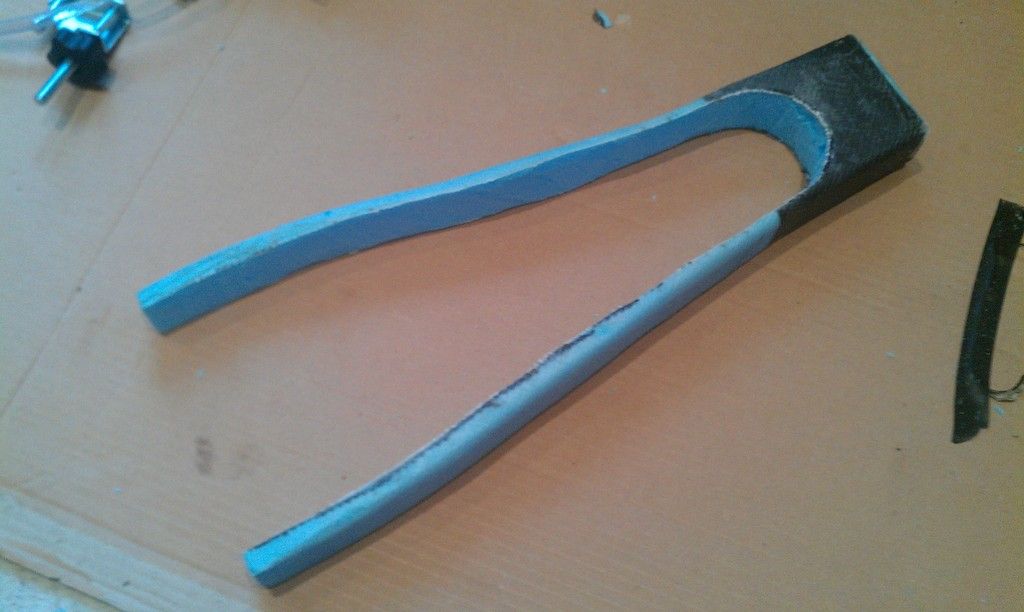
I’m still slightly undecided on how thick to make the downtube, I’m airing towards a 60 wide, 50mm deep oval (the full suss was 75-60mm oval)
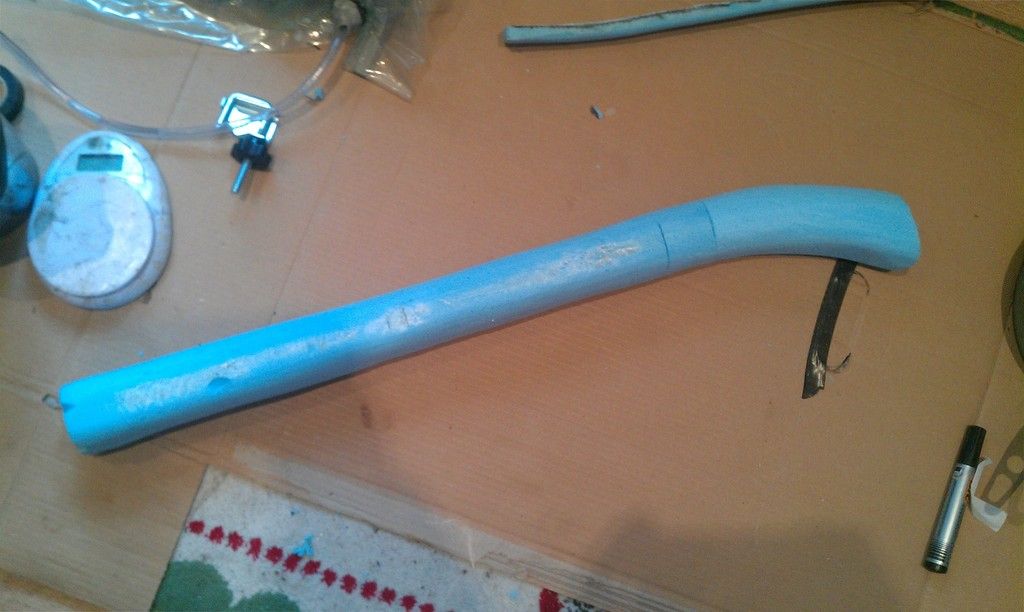