For anyone who has followed mountain biking for a decade or two, the fact that Hope has finally sat down and put together its own complete bike won’t come as much of a surprise. After all, the Barnoldswick-based manufacturer has been toying with the idea on and off for years.
Around a decade ago is when Hope really decided that it wanted to build its own bike. But back then the plan was to build a full-blown downhill bike, simply because that reflected the type of riding that most of Hope’s employees were typically riding. In fact, that’s kind of how the development of the bike moved from year to year. If the team rode DH, then that’s the bike they were interested in making. If XC became more popular, the aim of the bike shifted again. After going back and forth, the project settled somewhere in the middle – Hope was going to make an Enduro bike.
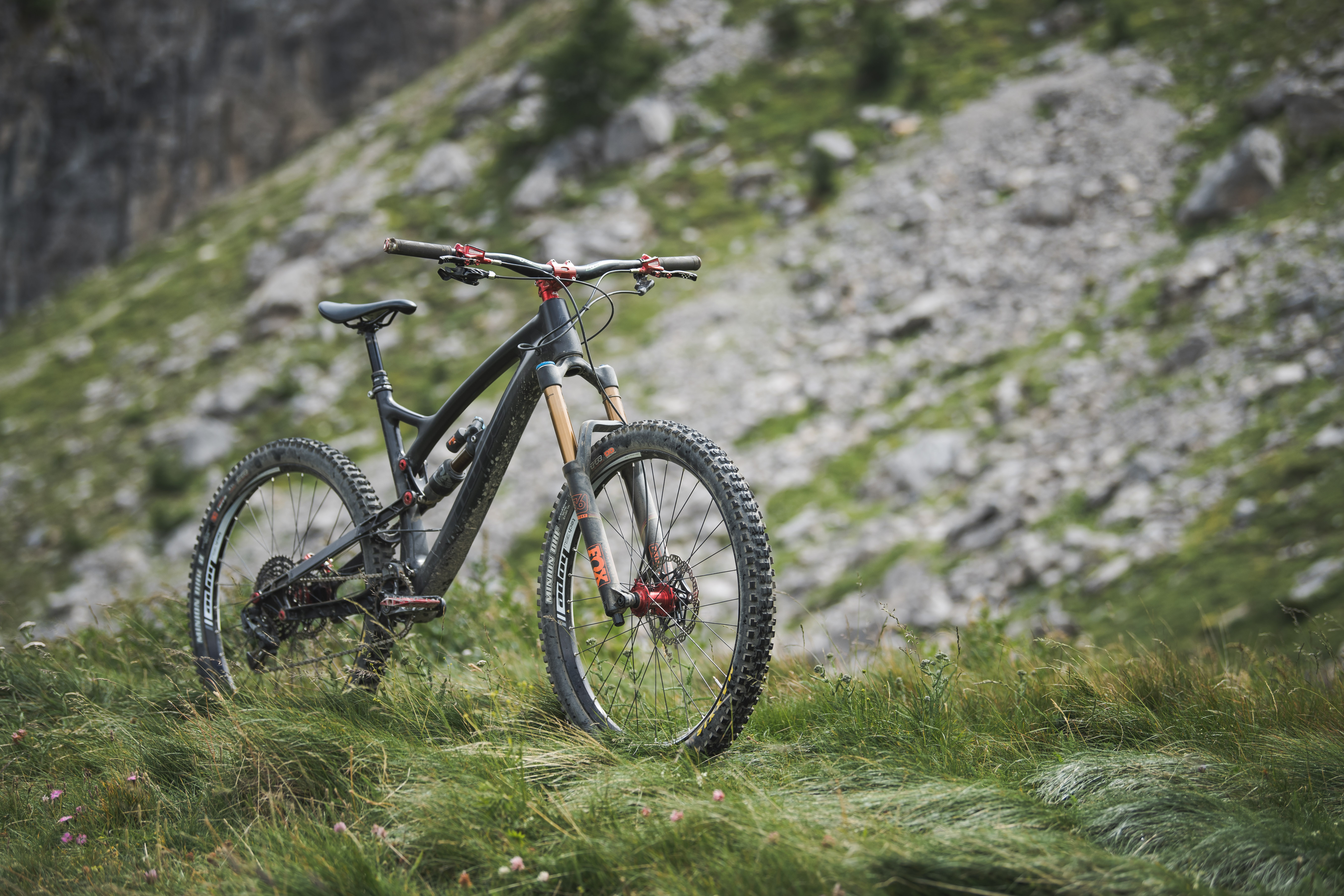
Originally the plan was to build an alloy bike that would basically be an internal workhorse and something that Hope staff could ride, but as the industry shifted towards carbon fibre, Hope realised that this was an area it could invest in, and so a carbon bike was penned.
At the same time as Hope shifted its sights to carbon, the industry was also moving to 27.5in wheels and fewer riders were chasing to use a front derailleur. These trends all helped to shape the prototype HB211 and ultimately, the production Hope HB160 that we see today.
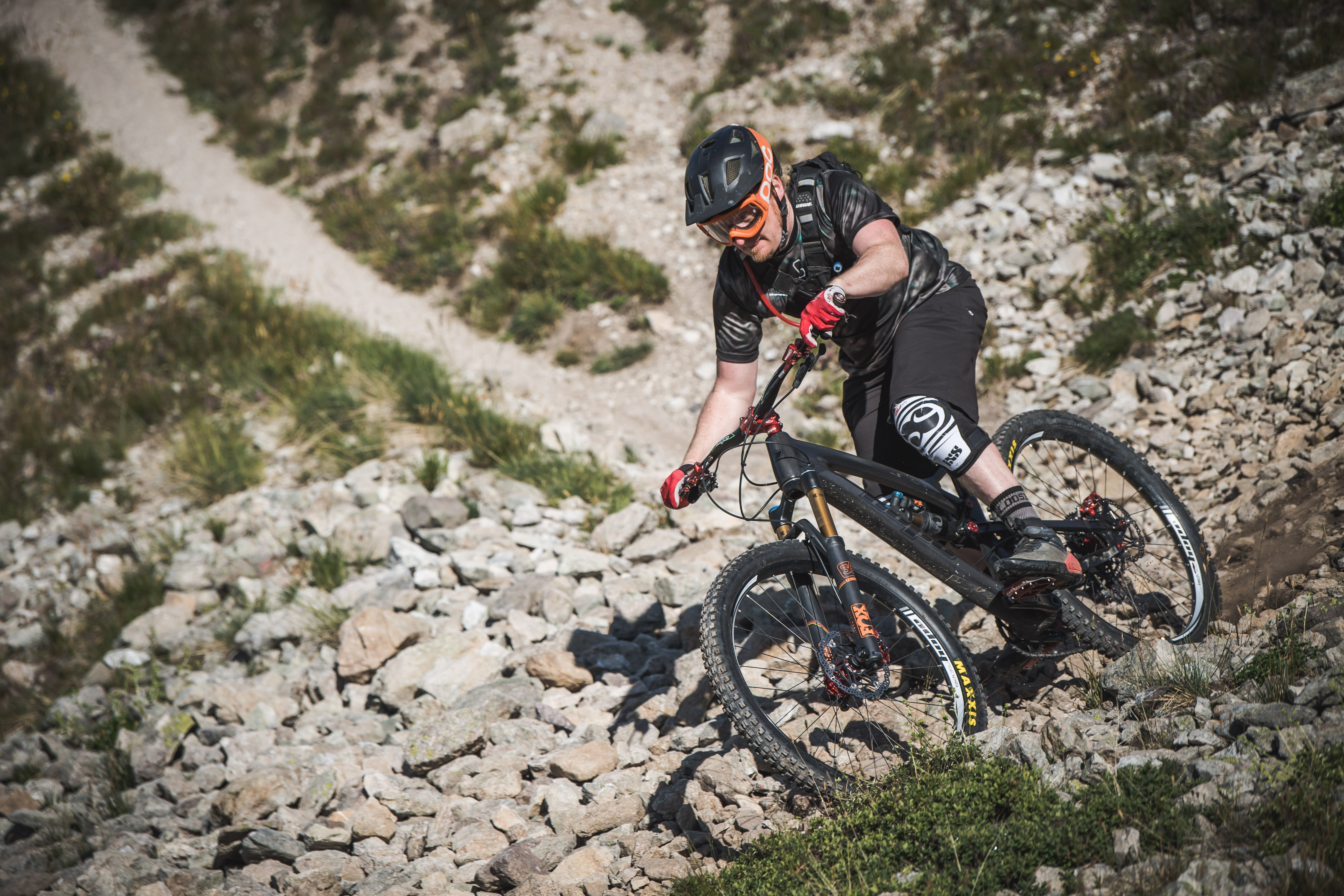
With Hope being an engineering company armed with decades of experience in CNC alloy products, it made sense to the company that they should build as much of the Hope HB160 as possible and that includes the moulds used for the carbon mainframe.
Each half of the alloy mould is machined in-house at Hope and takes half a week to complete. The mould itself is made up of a male and female mold that is finished to such a high tolerance that no filling or painting of the frame is required. Hope simply gives the final frame a light sanding and finish with an automotive lacquer, leaving the carbon weave on show.
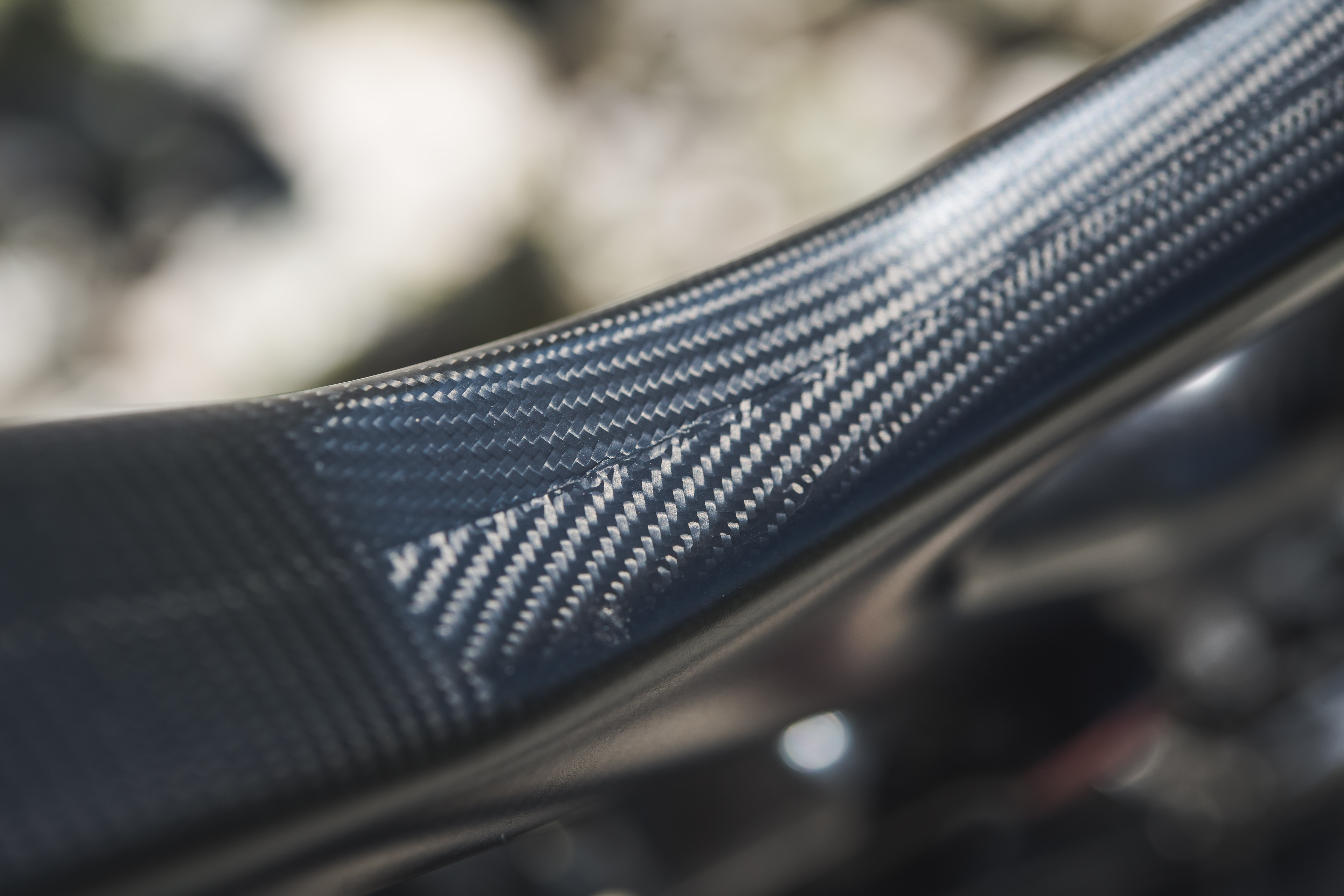
The main frame comes in S, M, L and XL sizing, and even now Hope is experimenting with the carbon layup to get the most from each frame. For example, the small sized frame has a slightly different layup to the larger frames in the range, which not only retains strength but also reduces the overall weight by 200-300g. These layups are still being tested though and we might see things change before the production bikes go into production, and even at this late date we’re seeing changes with the most recent being a reduction in seat tube lengths on with size M frames now being 5mm shorter and L, XL frames getting a 10mm reduction.
Interestingly the layup of the HB160 has been overseen by the same team that was put in charge of the bikes ridden by the British Cycling Track Team.
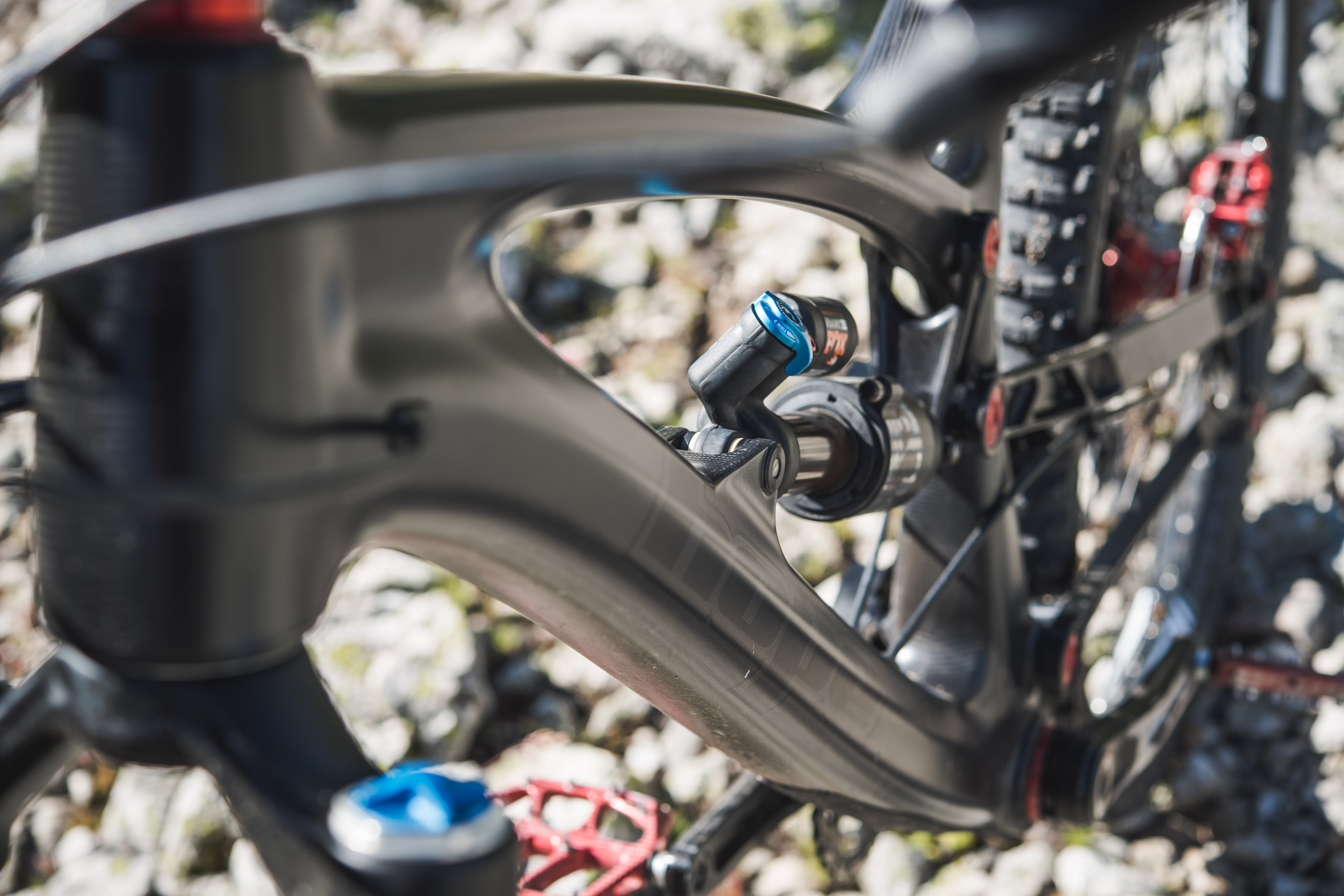
An oversized carbon down tube sits at the heart of the HB160 frame and gives the bike a sturdy core for the ride to push off through corners and over rough Alpine trails similar to those where we were invited to ride the bike for the first time.
It’s clear that, although the frame is carbon, Hope hasn’t manufactured it to be overly light weight. In fact, overbuilt springs to mind and I had no qualms riding the Hope on the ragged edge, over and through some of the types of rocky terrain that could easily see the end of a lesser bike.
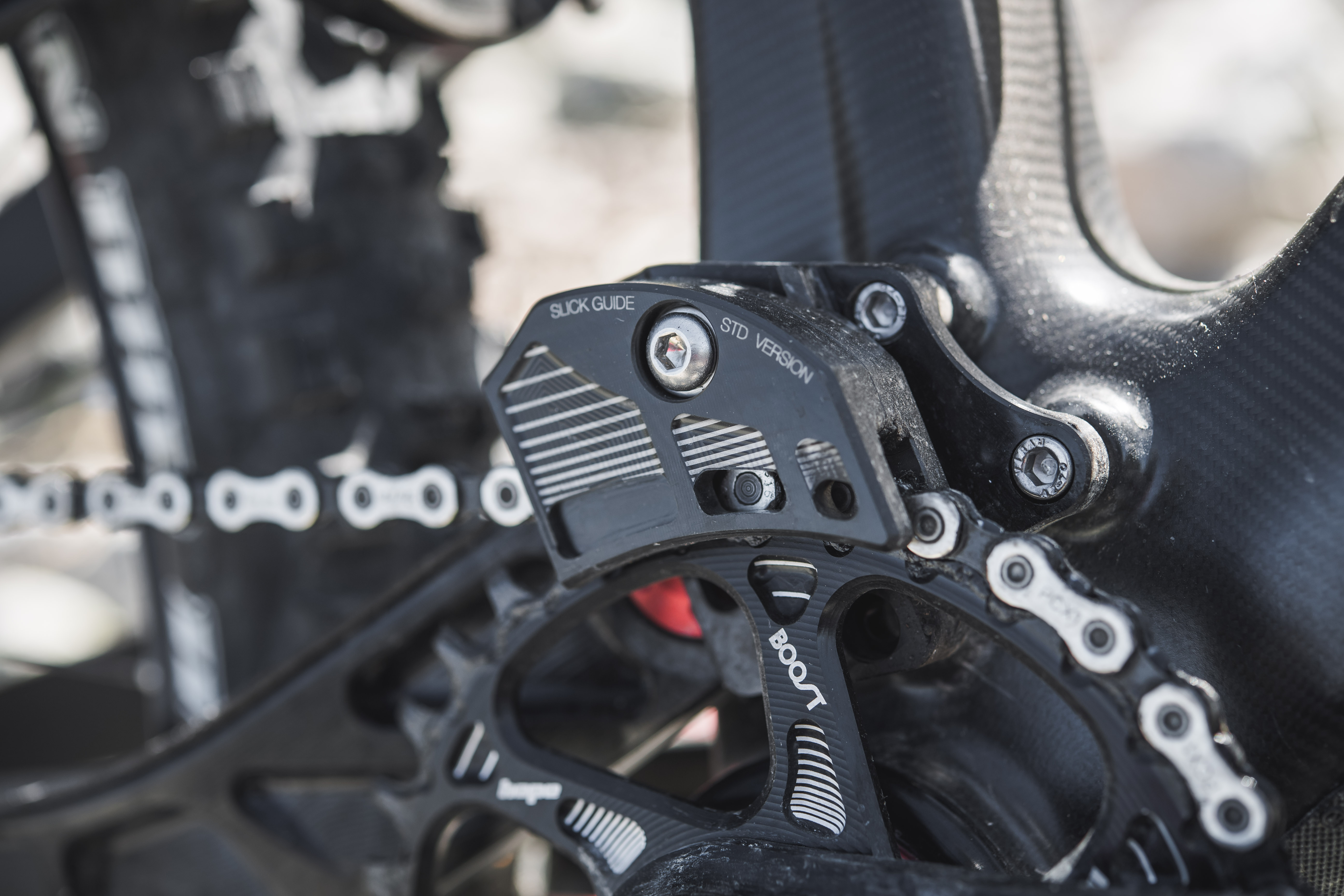
Keeping with the durable build of the HB160, Hope has engineered the frame to use internal alloy sleeves and inserts were required for bearings or bolts to attach to. While the bike doesn’t have mounts for a bottle cage, a neatly machined alloy insert has been created for a custom chain device to bolt to.
Alloy cups are bonded to the carbon mainframe so that bearings don’t touch the carbon, and all pivots except those for the top of the rocker are of the same size meaning you don’t need a handful of different bearings of various sizes with you when away on an epic summer alpine riding holiday.
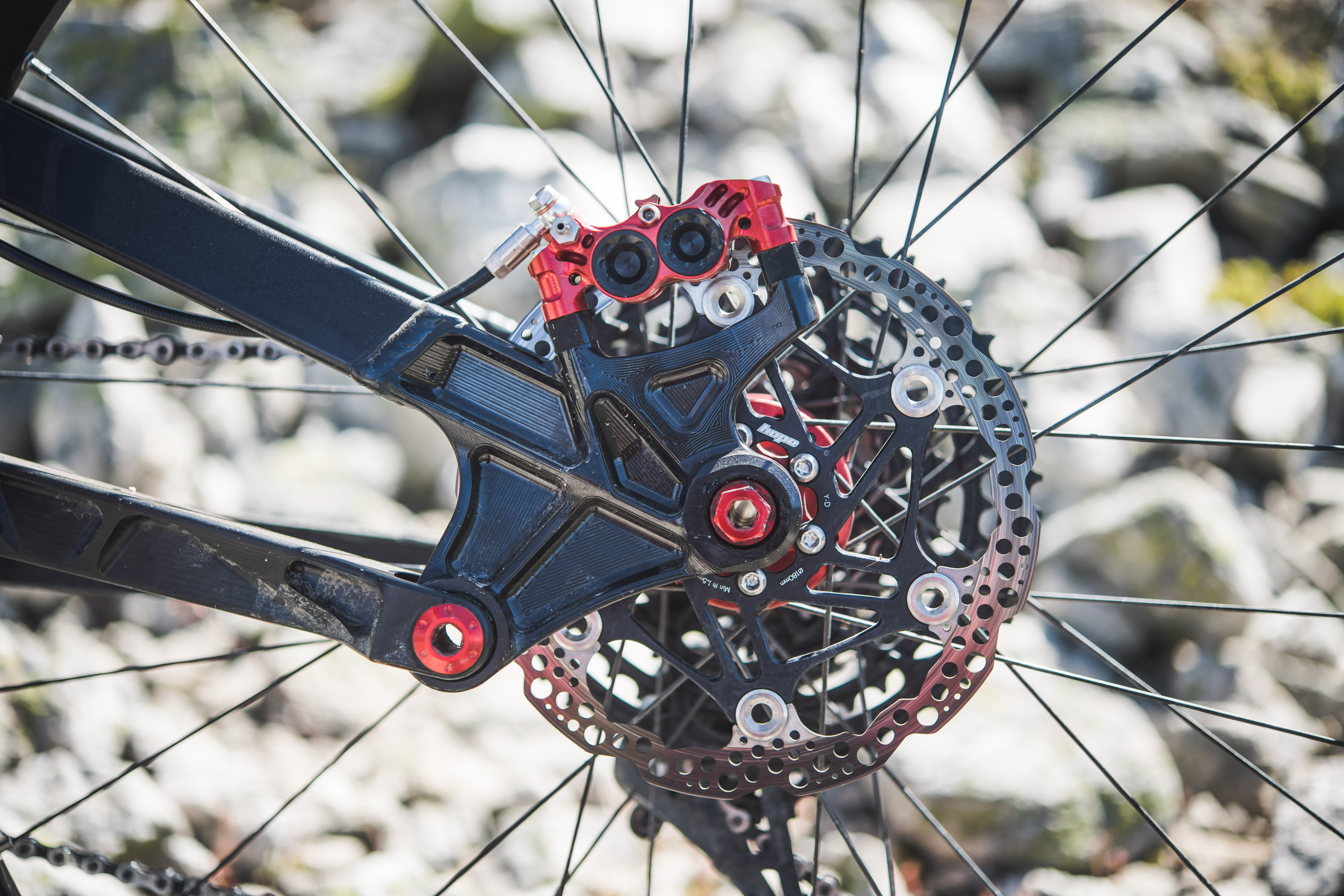
This being the first bike from Hope, the engineers decided that an alloy rear end would be a safe bet and it also gives Hope’s CNC marvels some time in the spotlight.
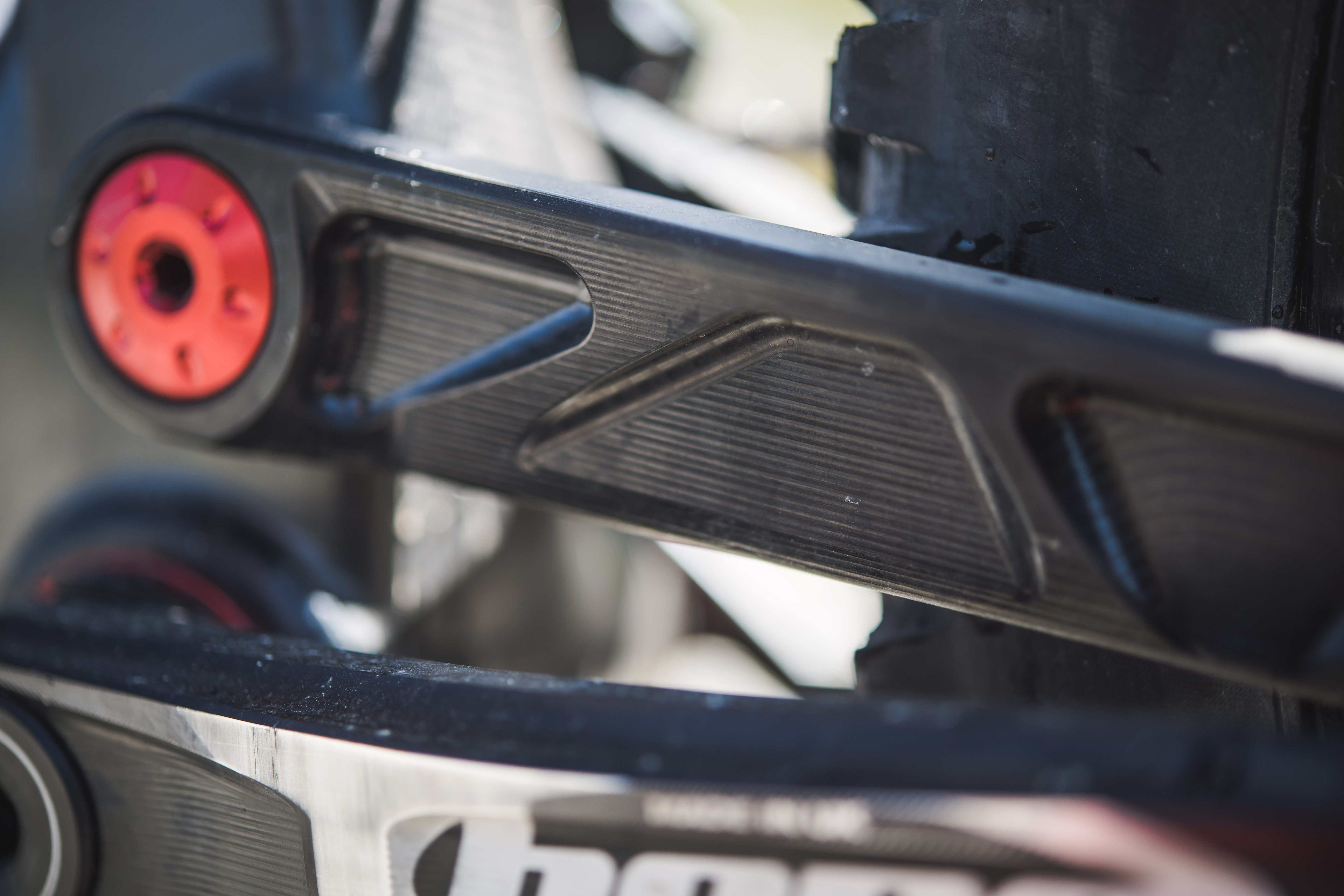
The progressive Horst link rear suspension connects to an alloy rear end that’s made up of a mix of tubing and carefully machined CNC parts. On our test bikes, these components were welded together, but Hope is planning to launch the HB160 with a bonded rear end. Moving to a bonding process will allow Hope to bring every aspect of frame manufacture in-house (they currently outsource the welding), and will also mean that a strong 2000 series alloy can be used in place of 6000 series. Bonding obviously also means that the rear of the frame doesn’t need to be realigned or heat treated after welding too.
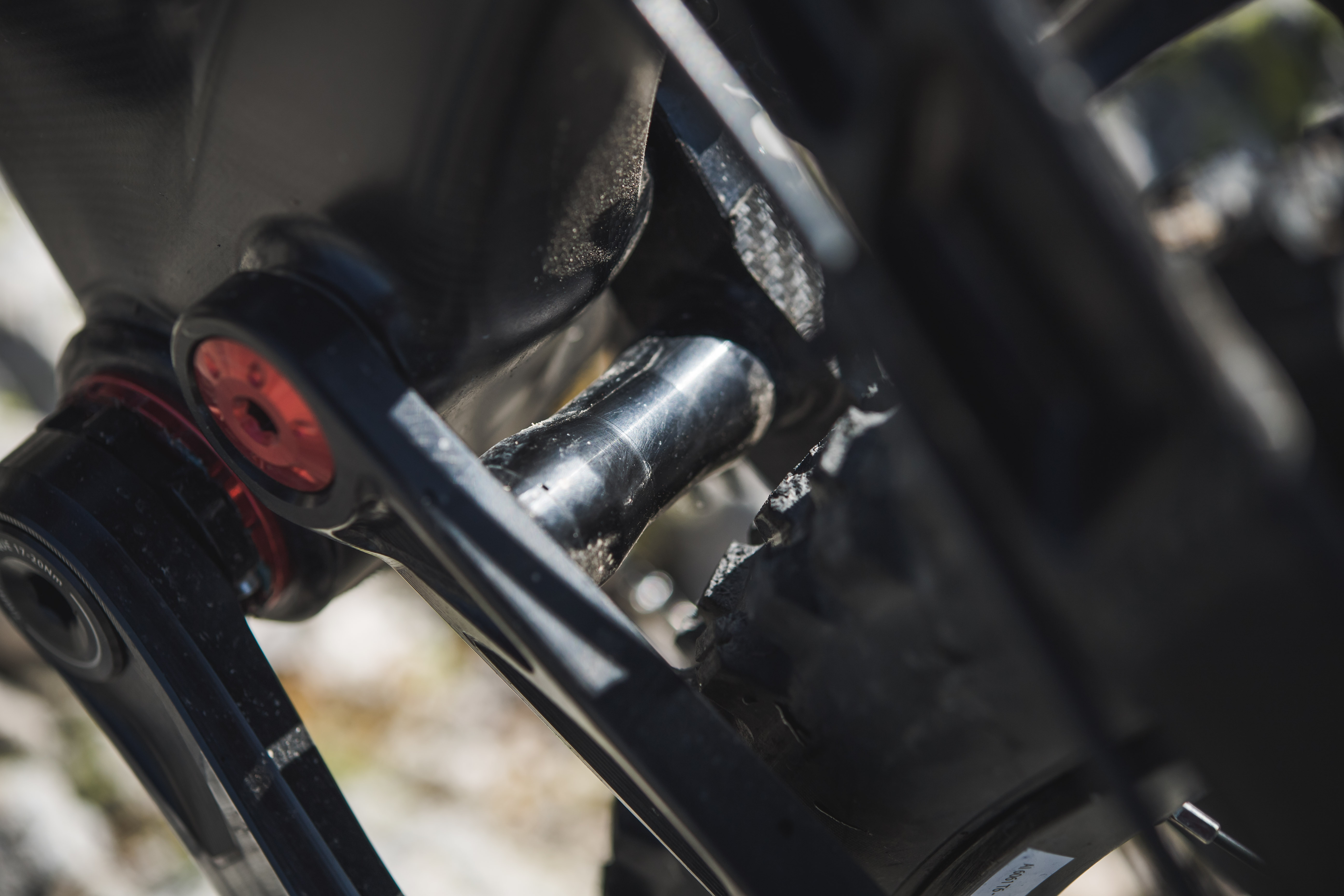
Hope’s designers also decided that building their own bike also gave them the opportunity to wipe the slate clean and build a bike that they had always dreamed about. This involved moving away from industry-wide standards in some cases and using ideas that would be unique to Hope and the HB160 in the pursuit of ultimate performance. Hope has stressed this wasn’t an effort to create annoying new standards, but rather a way to build a bike how Hope thinks bikes should be made.
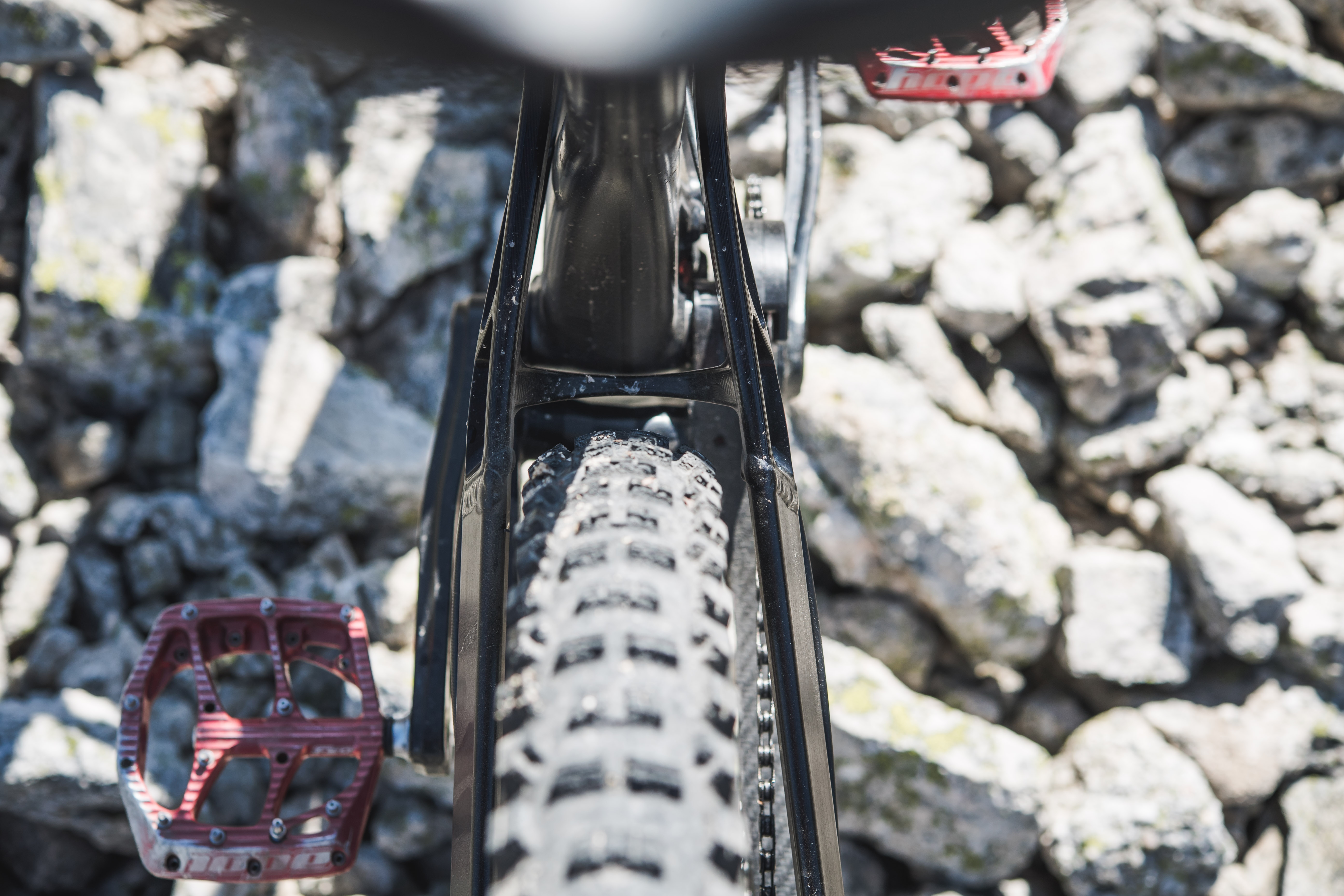
Or at least, this is the reasoning behind the super narrow rear end which sees Hope use a 130mm wide hub and massive 17mm thru axle. The concept was to create a rear end that would be less prone to hitting on trails obstacles while also decreasing the amount of side load on the rear of the bike to create a stiffer, and stronger backend.
To get the rear spacing as narrow as possible Hope has had to also redesign their rear hub for the HB160 and have done away with the internal axle on the hub. This meant that Hope could move to a thicker axle and means that once installed on the bike and tightened up the rear end isn’t going to go anywhere but where the suspension path leads it.
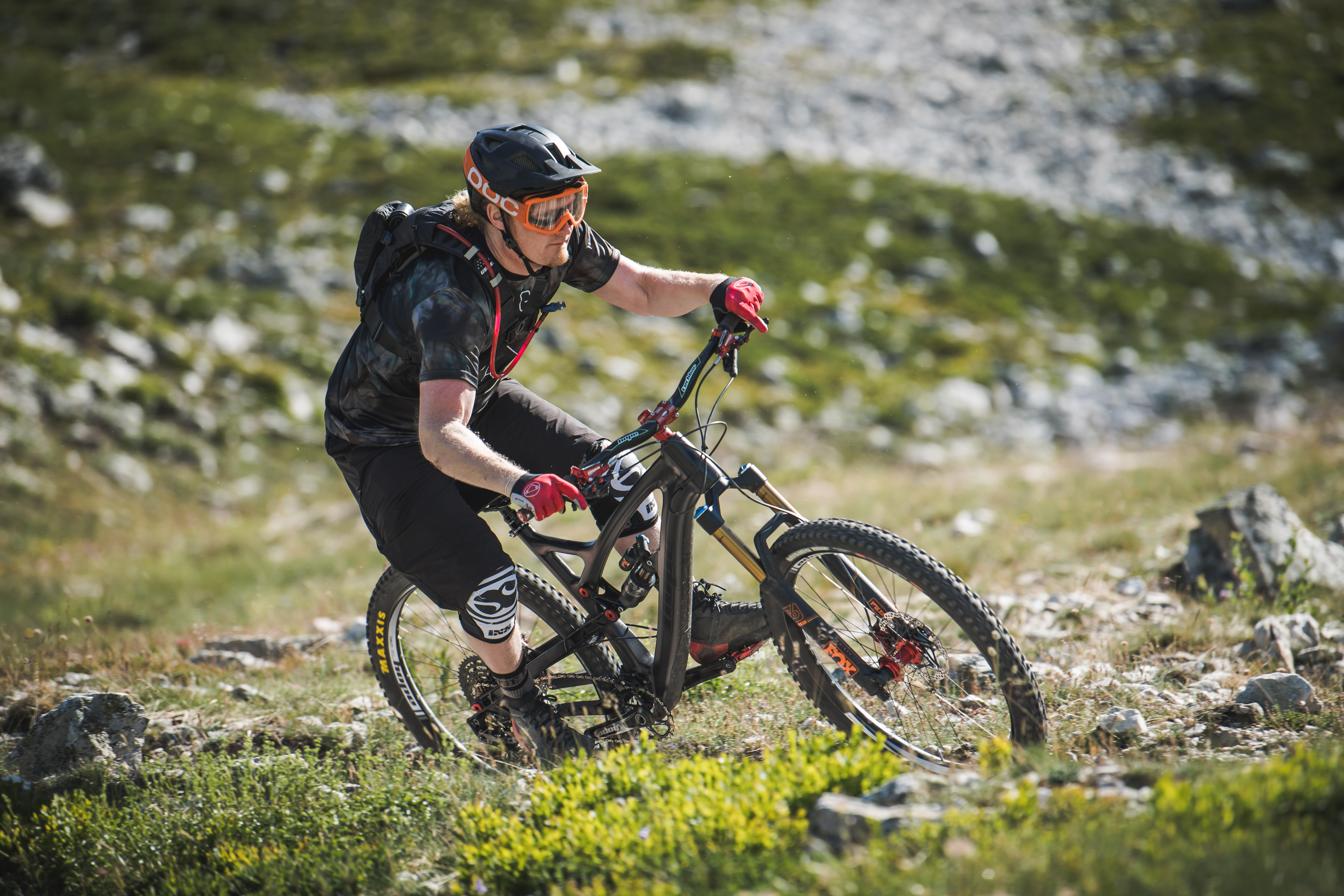
Hope also played around with the spacing of the rear hub and the positioning of the spokes to create a stronger wheel with less of a dish than traditional wheels. It’s similar to what we see with Boost on modern bikes, but on a much narrower overall package.
Another change we see on the rear of the bike is the inline disc mounts that are designed to attach to the frame in line with the rear axle. This basically allows for a neater mounting position and means that changing rotor sizes negates the need for overly complicated caliper mounts, instead all that’s needed is a simple ‘Lego Block’ spacer to move the caliper away from the axle. A small detail but a neat one.
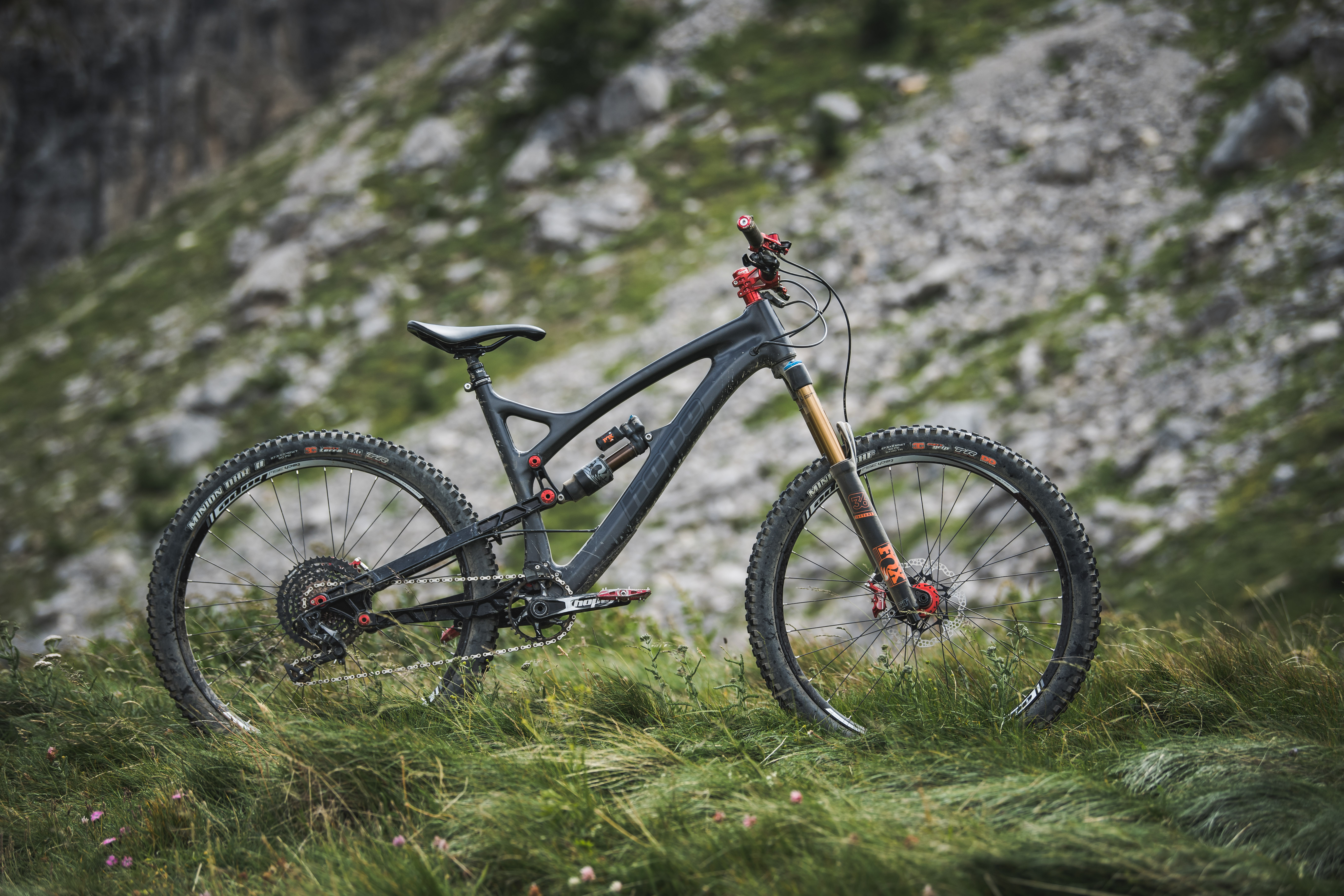
The suspension itself is a Horst link design chosen to offer a stable platform with minimal bob while retaining an active and playful ride. The production version of the Hope HB160 has 160mm of travel (10mm up from the original prototype’s 150mm of travel) and will use Fox Suspension front and rear – not Ohlins like the original prototypes were dressed with.
Being a Hope bike it’s not surprising to see that almost every component on the complete build is from the Hope stable. In fact, only the tyres, suspension, seatpost, rear mech and gear shifter don’t bear the Hope logo.
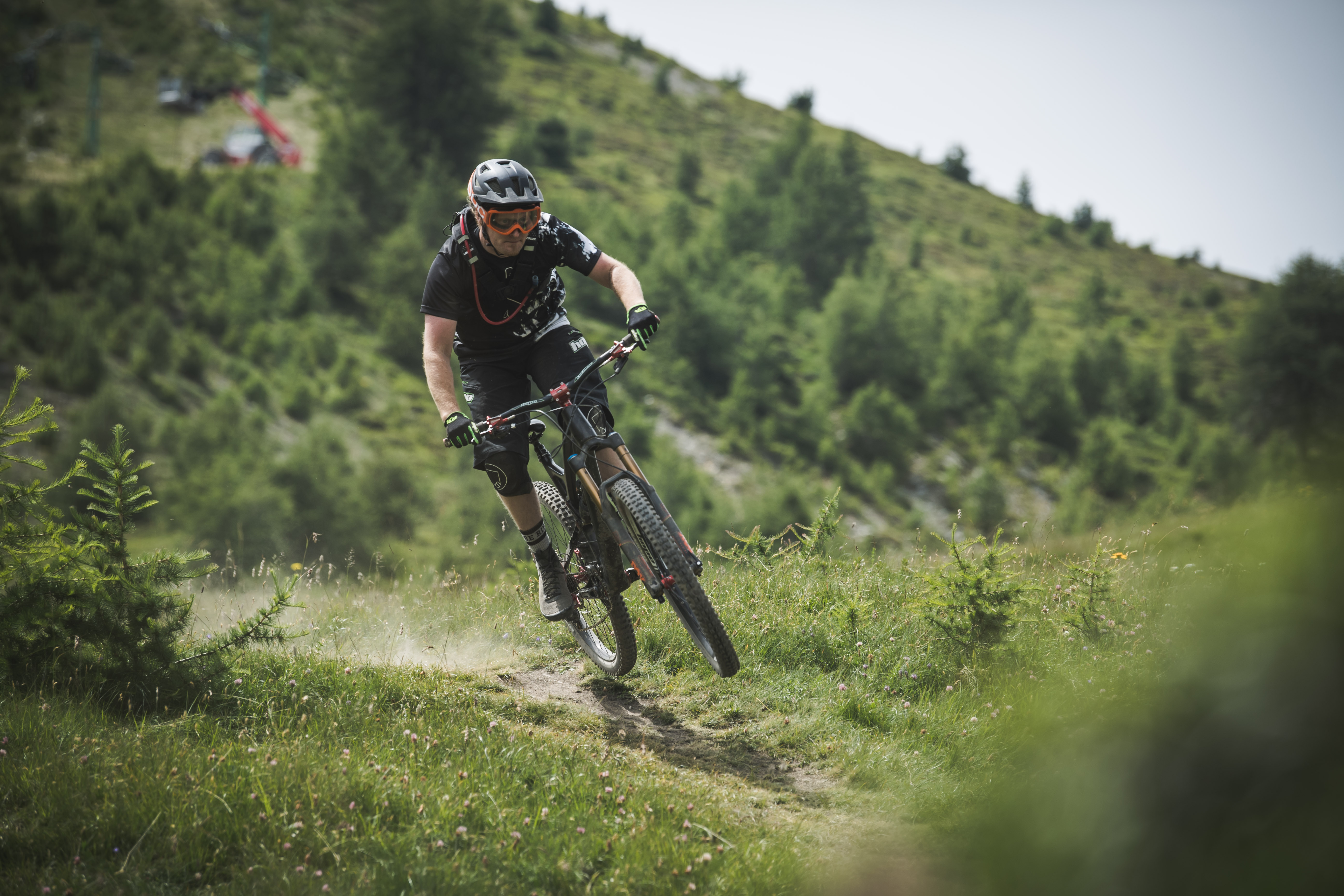
Hope brakes, crankset, hubs, bottom bracket, stem, headset, are all machined just across from Hope’s carbon facility all located in Barnoldswick, making it the most British, British built bike on the market today! Even the carbon is manufactured in the UK (just down the road).
So what does a Hope HB160 cost you, and where will you be able to buy one from? Well, only one model of Hope HB160 will be available with the only options being the size of the bike and the colour of the Hope components used to complete it (seven colour options in total) and that will cost £7,500.
Hope will only be offering the HB160 as a complete bike and to begin with customers will have to buy the bike in store through 1 of 10 selected physical retailers (these are unconfirmed at the time of writing) or from Hope itself.
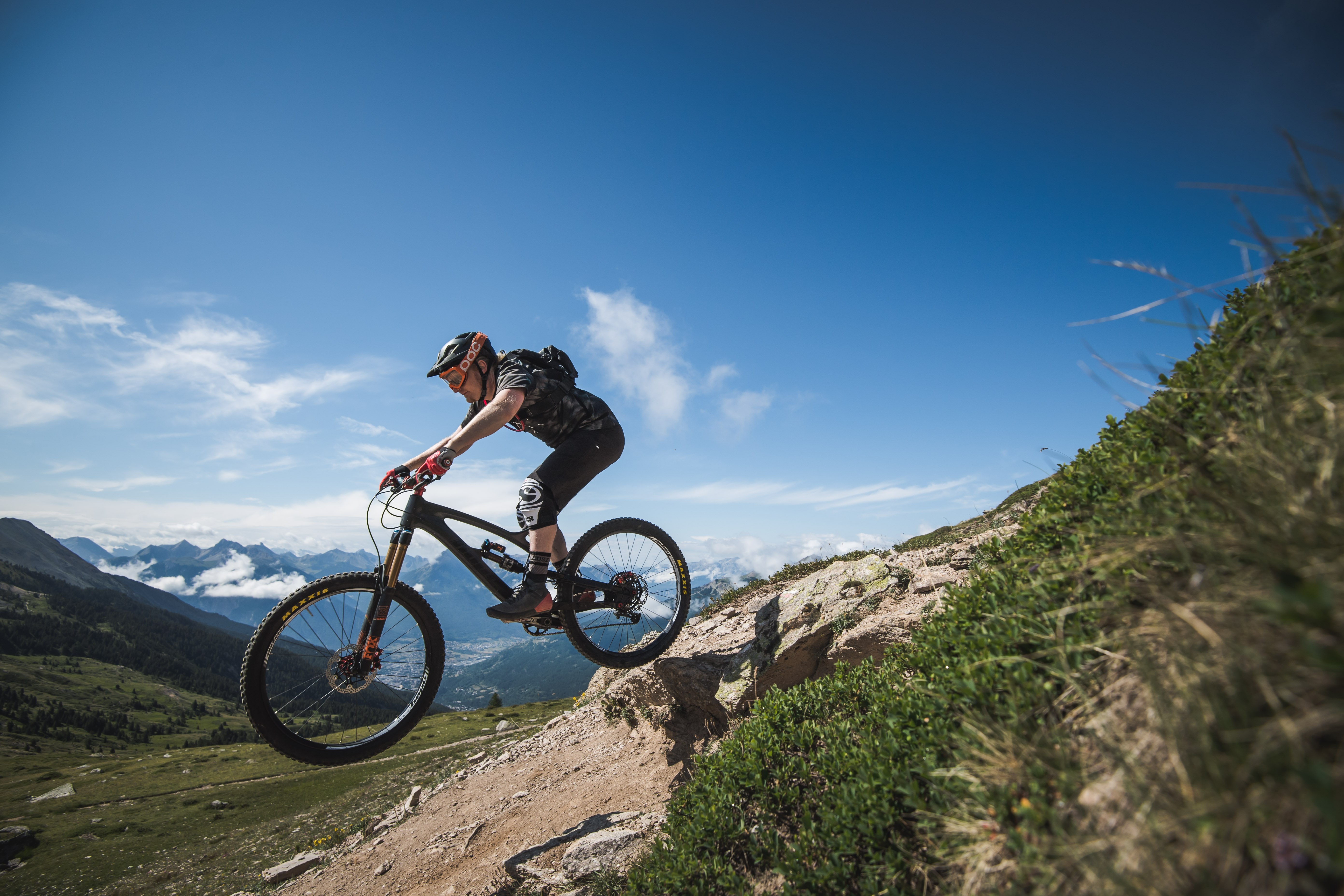
Numbers will be highly limited too as Hope only plans to manufacturer around 500 bikes per year or around 10 per week.
If you’re not in the UK and fancy the Hope HB160 then not to worry as there are plans to release the bike in other markets too. After the UK, Hope has plans to launch the HB160 in France and Germany, again through select retailers, then in January 2018 customers in the U.S will also be able to purchase the bike. At this point in time, we don’t know what pricing outside the UK will be.
So there you have it, the Hope HB160. What do you think of this very British bike? What do you make of the pricing? And are you likely to buy one? Let us know in the comments below.
Vote In The 2017 Singletrack Readers Awards Here.
Comments (9)
Comments Closed
“the layup of the HB160 has been overlooked”
Don’t you mean overseen? A bit scary if they’re overlooking the layup as I’d have thought it’d be pretty important!
i wouldn’t be surprised. british cycling overlook all sorts these days
Fixed 🙂
Thanks…
So what’s the ride like?
So Hope are saying boost spacing is a loada tosh . Good on yer!
Well, that’s very interesting. It must be really exciting for such a small team to have so much freedom to design something like that around custom parts.
£7500 Bloody hell, its got to be a lot of bike to justify that
Didn’t Hope say in the past it would be cheaper to make a bike in the UK? Shame they’ve gone large with the pricing.
Nice. I think that they’ve gone with the seriously premium bike price tag to gain a that ‘premium bike’ cache – and justifiably so. It will have been a fairly expensive thing to R&D and manufacture so far. Nevertheless, it still looks pretty competitive against the other halo bikes out there. It’ll definitely find a niche.