These days, the mountain bike wheel game must surely be a hard one to crack (boom-tish!). But seriously, unless you’re a big brand with a suitably big marketing budget, you’ve really gotta offer something genuinely unique. Something eye-catchingly different. Something that stands out from the pack and shows that there may just be an alternative to the status quo.
But us cyclists are sceptical people. And to be fair, we can be pretty stubborn too. I mean, when you’re talking about wheels, how different can a new product be from what has already been tried before?
If you were a Luddite, you’d be pretty happy with how the bicycle wheel has panned out thus far. But people like Mello Bouwmeester aren’t luddites. They’re innovators. And thankfully for us, they’re never happy with the status quo.
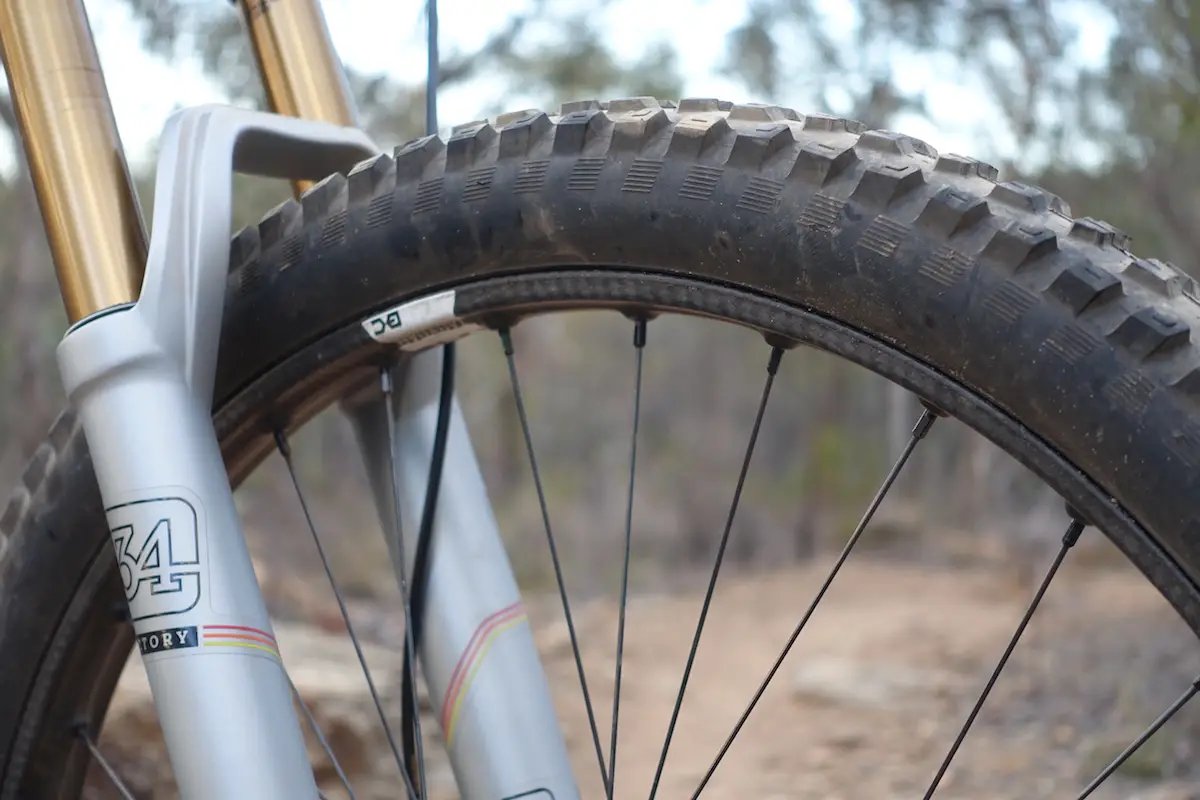
Australian Innovation
Spearheaded by Mello Bouwmeester, Bouwmeester Composites (BC) is a small Australian manufacturer based out of Adelaide. Despite its diminutive size, the fledgling company is making big waves in the international mountain bike scene thanks to its brand new Tammar V4.8 wheelset.
Designed for Enduro racing and hard-core trail hammering, the Tammar is based upon a full carbon fibre rim that has been designed, engineered, tested and manufactured in Australia. Given that only ENVE and a few other small companies choose to manufacture carbon rims outside of Asia, that fact alone is a worthy point of difference. However, there’s a whole lot going on under the Tammar’s hood that has generated significant media attention all over the globe.
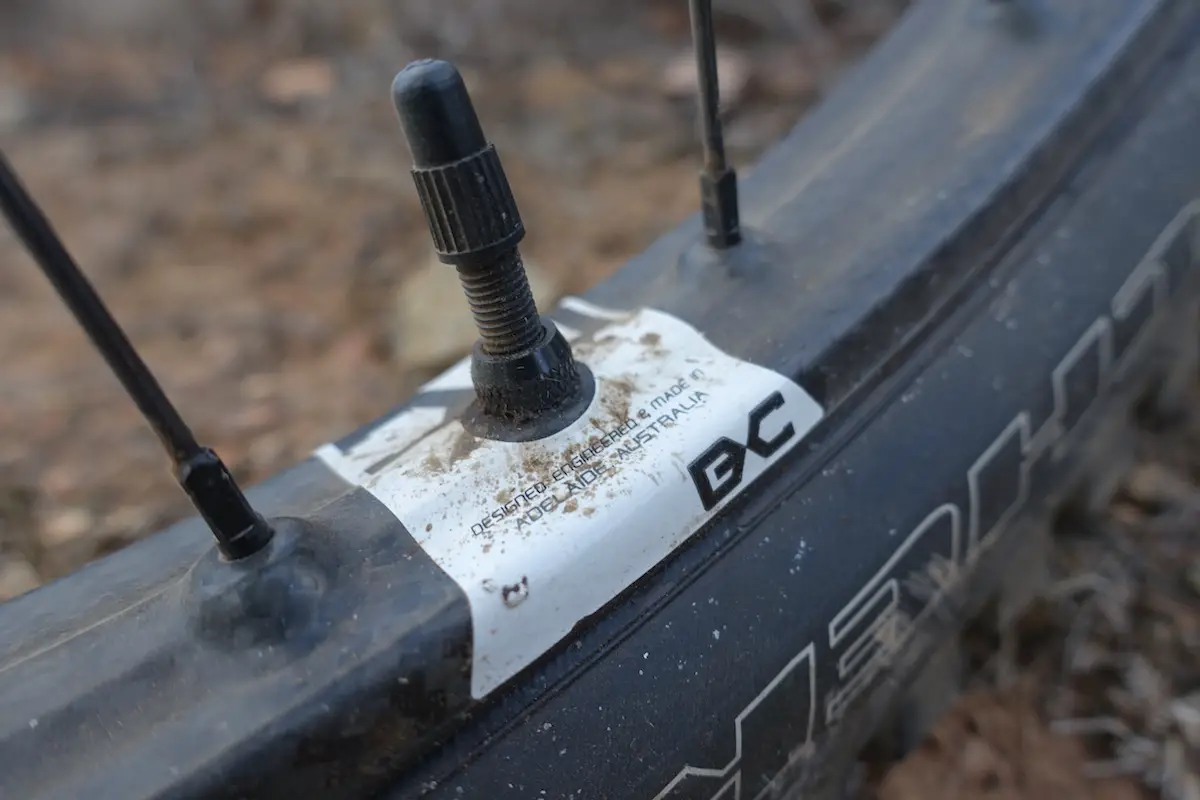
The wheelset features a wide rim profile, tubeless compatibility, and a standard 32-spoke build with DT Swiss hubs and spokes. With a claimed weight of 1780 grams, the Tammar wheelset is targeted towards Enduro racing and hard-hitting trail riders. Currently, it is only available in a 27.5in diameter.
As homage to their Australian roots, BC named the Tammar after a small wallaby (it’s like a kangaroo, but smaller eh?) found in South Australia. This fast and nimble marsupial almost went extinct many years ago, but a successful conservation program as seen healthier numbers return. Its story is a little bit special, and BC reckon the Tammar wheelset is pretty special too.
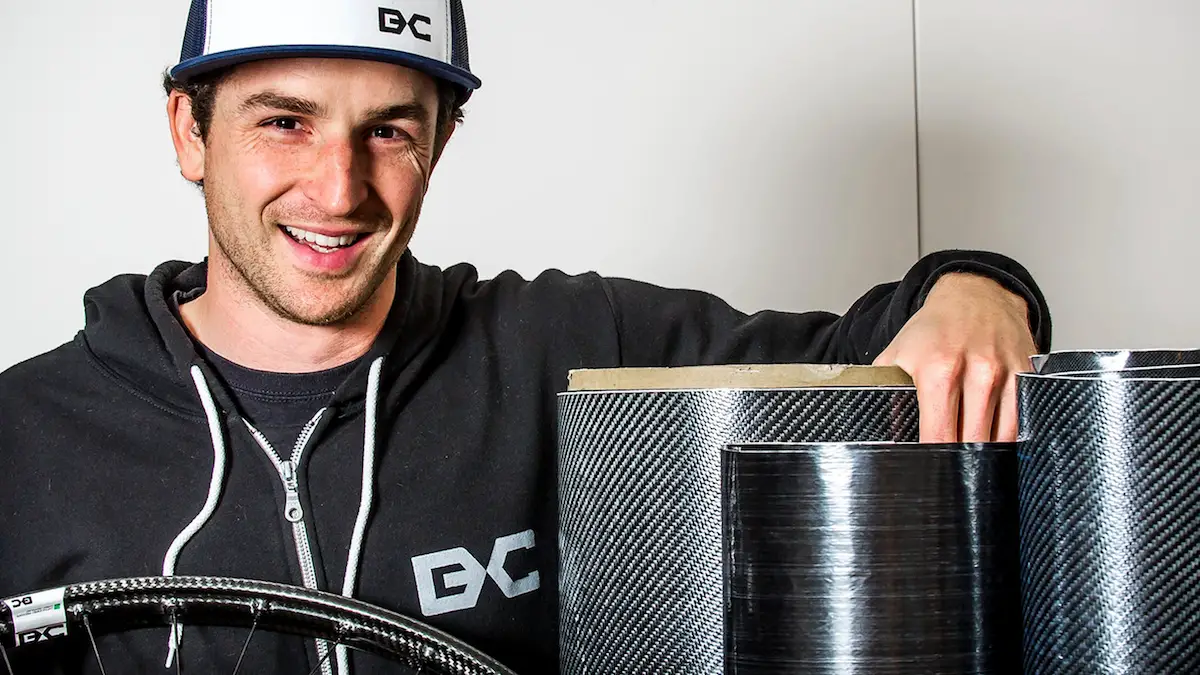
The Master Builder
With 18 years of experience working in the cycling industry, Mello Bouwmeester is as deep in it as you can get. Having worked across the retail, wholesale, service, design, racing, and manufacturing sectors, this is a man whose life is entirely invested into all facets of the bike scene.
Mello first formed Bouwmeester Composites (BC) back in 2008, where he began by building superlight road racing wheels out of his workshop using carbon rims he had manufactured to his design specs offshore. Locally and abroad, the reputation for both Mello’s wheel building skills and for his product grew quickly. It is perhaps quite fitting then that in Dutch, his last name translates to ‘Master Builder’.
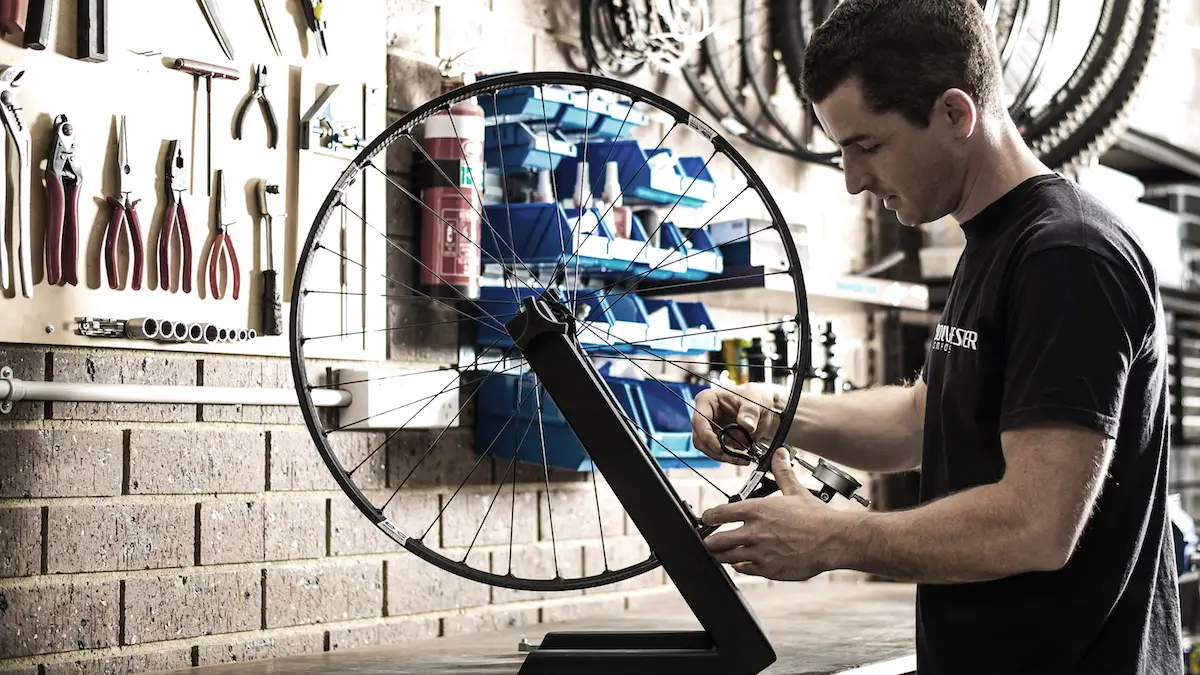
Since 2008, carbon wheels have not only flooded the road scene, they’ve also pervaded into the mountain bike market too. These days nearly every wheel brand offers a carbon variant, and surging demand for plastic-fantastic hoops has seen many new markets open up, including cheap direct-to-consumer product coming from China. For better or worse, carbon wheels have never been as accepted or as accessible as they are right now.
As carbon wheels have transitioned from niche to necessity for mountain bikers, Mello began turning his attention back to the dirt. Despite the popularity of his road wheelsets, he had big ideas swimming around in his head, and he had even bigger plans on how he was going to make those ideas come to life.
And so in 2012, Mello made the decision to relaunch the company with a renewed focus on R&D that would take him back to his roots. The ultimate goal? To design and manufacture his own unique off-road carbon rim on home soil.
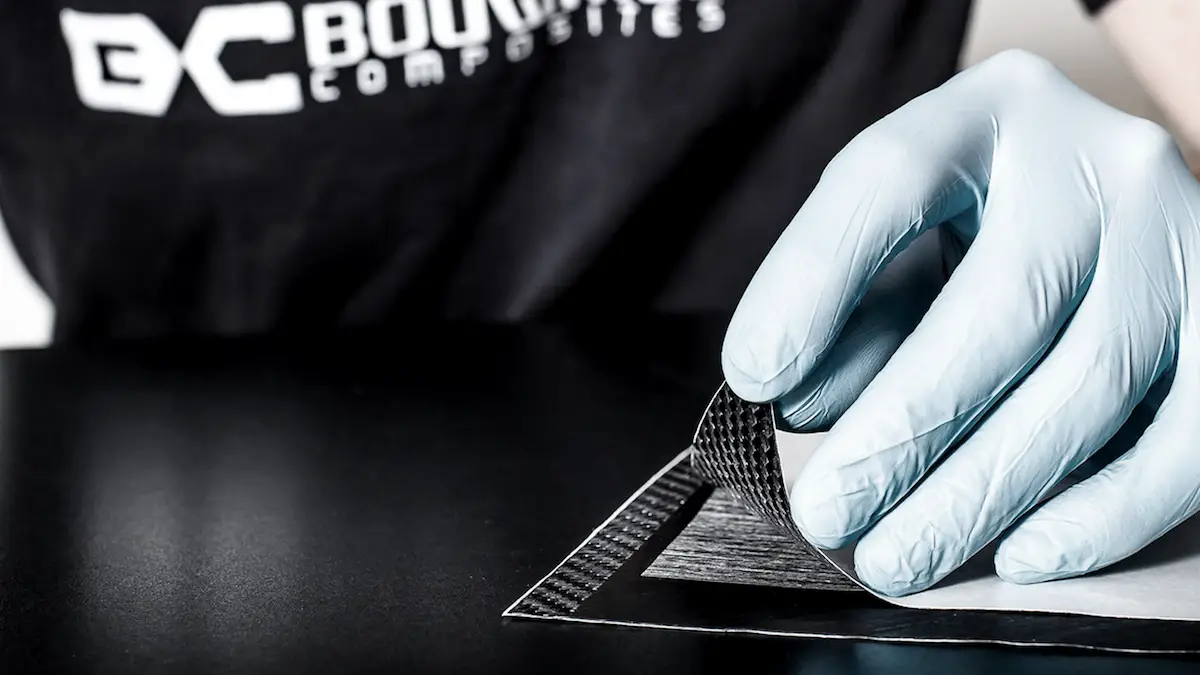
The Second Chapter
After riding the Tammar wheelset for several weeks, I had the opportunity to sit down with Mello and find out more about the development behind the wheels. “Absolutely”, Mello tells me when I ask him if he sees two different chapters in his company’s history. “Bouwmeester as it was known then is very separate from what Bouwmeester Composites the company is about today”.
For Mello, it seems that only the name remains the same. The product, the design and the execution however, are all very different. “Today BC product is 100% Australian designed, engineered and made. This transition to Australian manufacturing is something I’m very proud of. It gives us better capacity as a business with our IP, design, research and quality control.”
Many riders out there will be stoked on the option of an Australian-made product, but it isn’t quite as easy as you’d expect. There’s a reason why most of Mello’s competitors simply re-sticker catalogue rims made in the Far East.

“It took us about 2 years to develop the current Tammar rim” Mello explains. This extensive development process was undertaken with the help of specialist composites firm Luescher Teknik.
As a carbon specialist with experience working in aerospace, Raoul Luescher is one of the only engineers in Australia certified to perform carbon fibre repair on Air Force fighter jets. He’s also a passionate cyclist, and is well known as being the go-to man in Melbourne for carbon bicycle frame and component repair. Having an enormous database of information about common carbon failure points and fracture behaviour to draw from, Mello and Raoul took full advantage of this data during the Tammar’s development and testing phase.
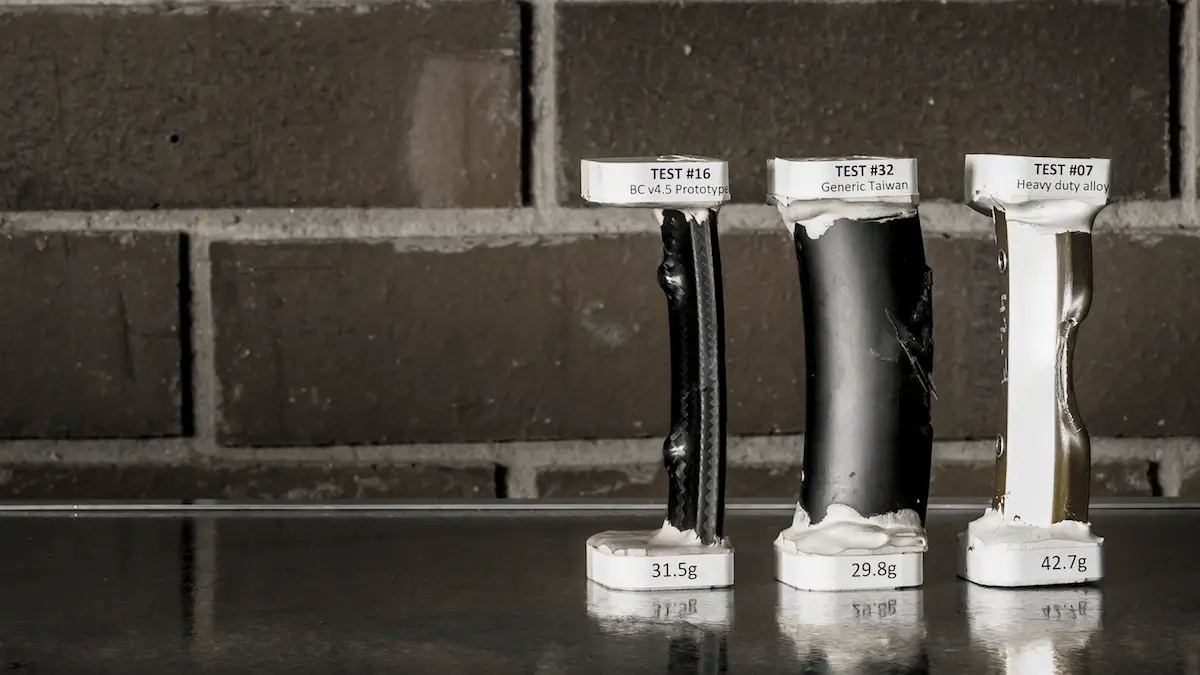
“The Tammar was really a back to basics approach with rim design and a look at fundamentals to make a better product”, Mello explains when I ask what drove the need for a new rim design. “We also listened to customers talk about the harsh and unforgiving feel that stiff larger box section carbon rims give when on the trails. This took us down a very interesting R&D path for optimising and tuning the layup in our rims to offer more compliance, better grip and handling”.
And does Mello have an idea of how many hours have gone into the final product?
“It would honestly be scary to add up!” he admits with a laugh. “I’m probably lucky to still have friends and family, as often I’d be in the workshop close till midnight, every night. Just for our final layup we made over 50 variants, and we backed that up with the accompanying barrage of tests to validate it. This was just one very small portion of the total project”.
The result of BC’s two-year development program is the Tammar V4.8 wheelset. The number in the name refers to it being the 4th generation rim design, and the 8th layup of that final profile.
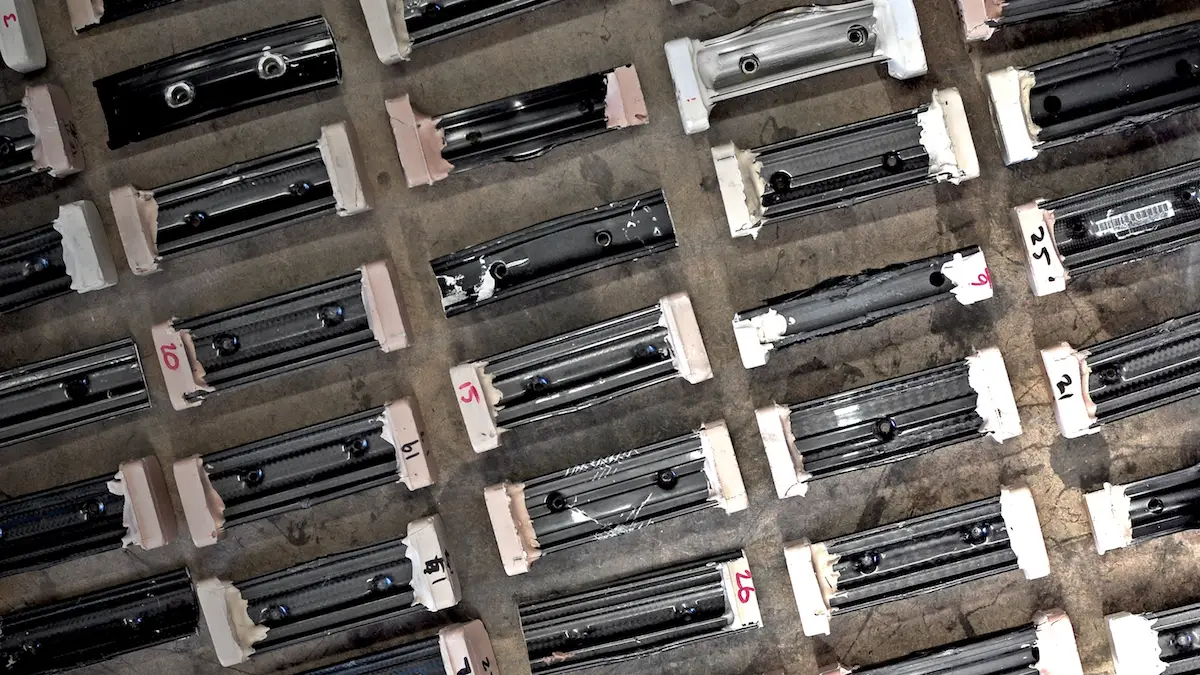
Developing the perfect rim
Designed and built as the ultimate 27.5in Enduro wheelset, the Tammar features a 38mm wide carbon rim, with a unique single-wall design that’s not unlike a motocross rim. “Interestingly, it was less driven by inspiration and more focused on the process of design, testing, validation and research and development” Mello explains when I ask him where the inspiration came from for the single-wall design.
Unlike other carbon rims that are hollow, the Tammar rim is solid from bead to bead. Each sidewall is 3.25mm thick, and the rim bed is even thicker. This solid-wall design builds on the strengths of carbon fibre, which is at its toughest when made up of many interlaying levels that are firmly compressed together.
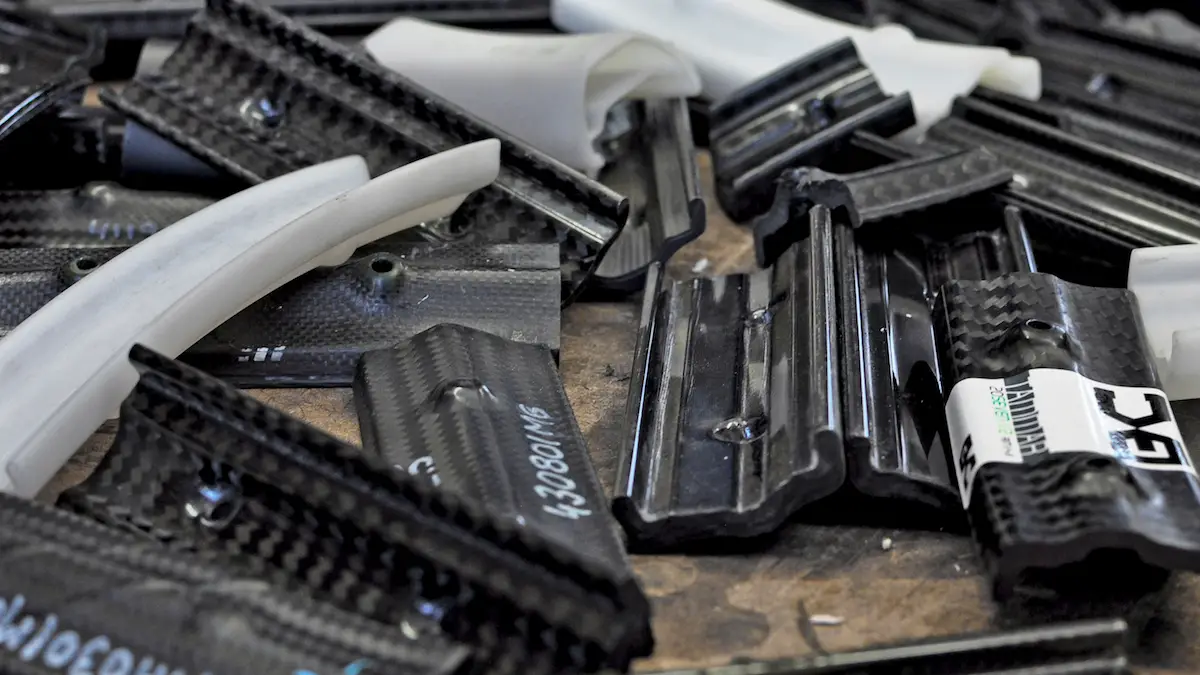
“Quite a lot of carbon box section rims go down to about 0.9mm through the mid profile”, explains Mello, who spent an enormous amount of time conducting destructive testing of his competitor’s products. “All current carbon rims on the market are just a carryover from road rim design or aluminium extrusion profiles”, Mello informs me. “While there are some design tweaks, they are not fully optimised for composites. One impact from a wayward rock and it’s party time for delamination at those thicknesses”. In comparison, the thicker laminate of the solid Tammar rim is capable of being far more tolerant to impact damage.
BC sources premium TorayCA carbon fibre, with an enormous number of plys laid up in each rim. They use a toughened resin matrix blend, which contains microscopic rubberised particles that help the rim to absorb impact energy to reduce the chance of cracking.
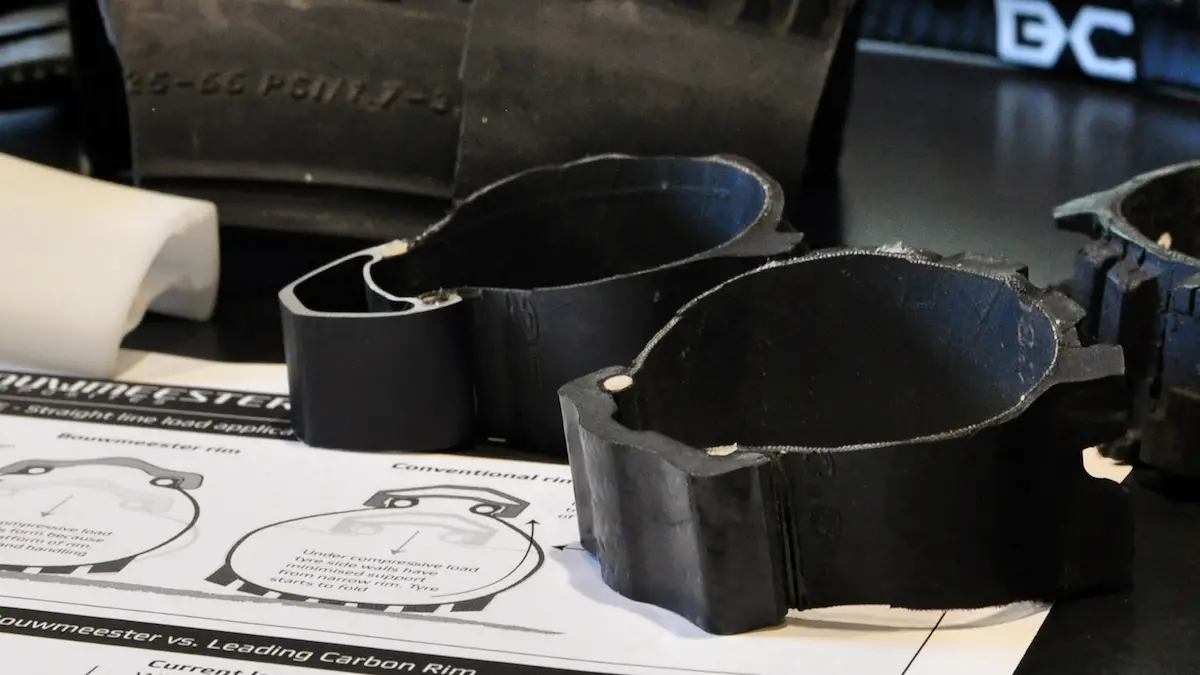
Because the rim isn’t hollow, BC is able to use mammoth pressures during the curing process. While standard carbon production sees pressures of about 120psi, BC uses over six times the level of compaction to create a more dense and void-free structure. This is what gives the Tammar rim its enormous strength.
“It’s a fairly intricate and time-consuming carbon layup and manufacturing process”, Mello responds when asked about the number of hours that go into producing each rim. “Even down to our spoke holes, we use a special aircraft certified drill piece for accuracy, because poor drilling practices can create delamination at the critical point of spoke load. We also drill on two-axis, which is matched to our CNC machining of the mould, so the nipple sits at the perfect angle in the rim”.
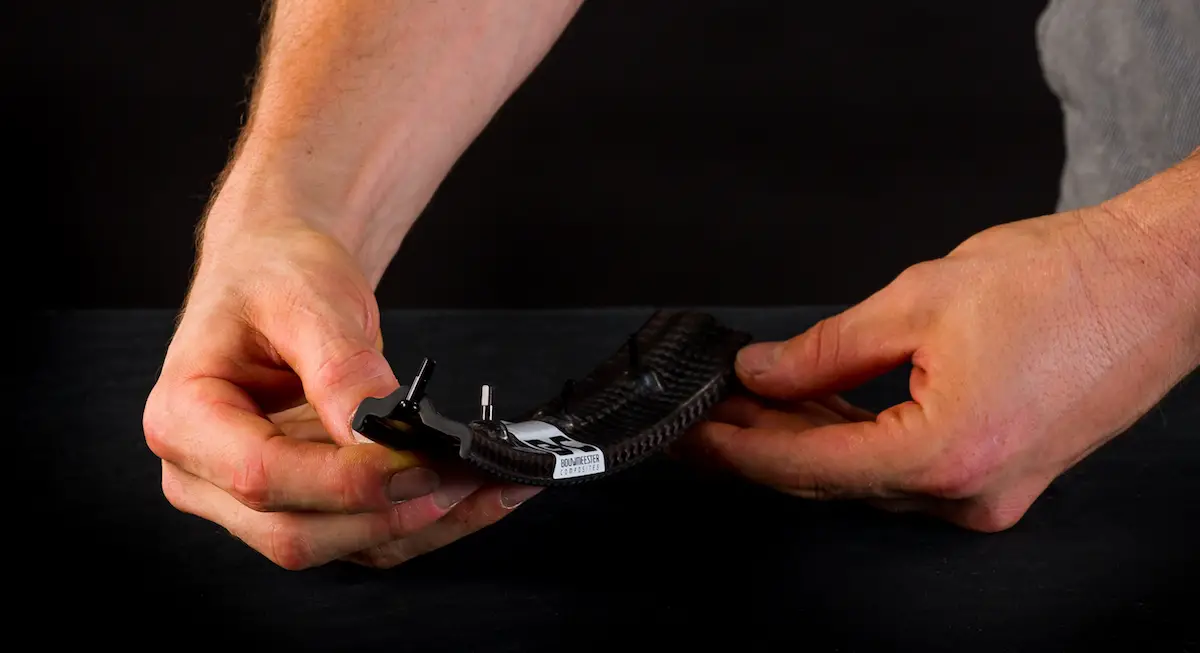
Initial Impressions
On every ride with the Tammar wheelset, I could never get far without someone stopping me to ask what they were. With their shallow profile and bulging moulded nipple beds, the carbon Tammar rims offer a unique aesthetic that bucks the current trend of super deep-section carbon rims and their “LOOK AT ME” fluoro graphics.
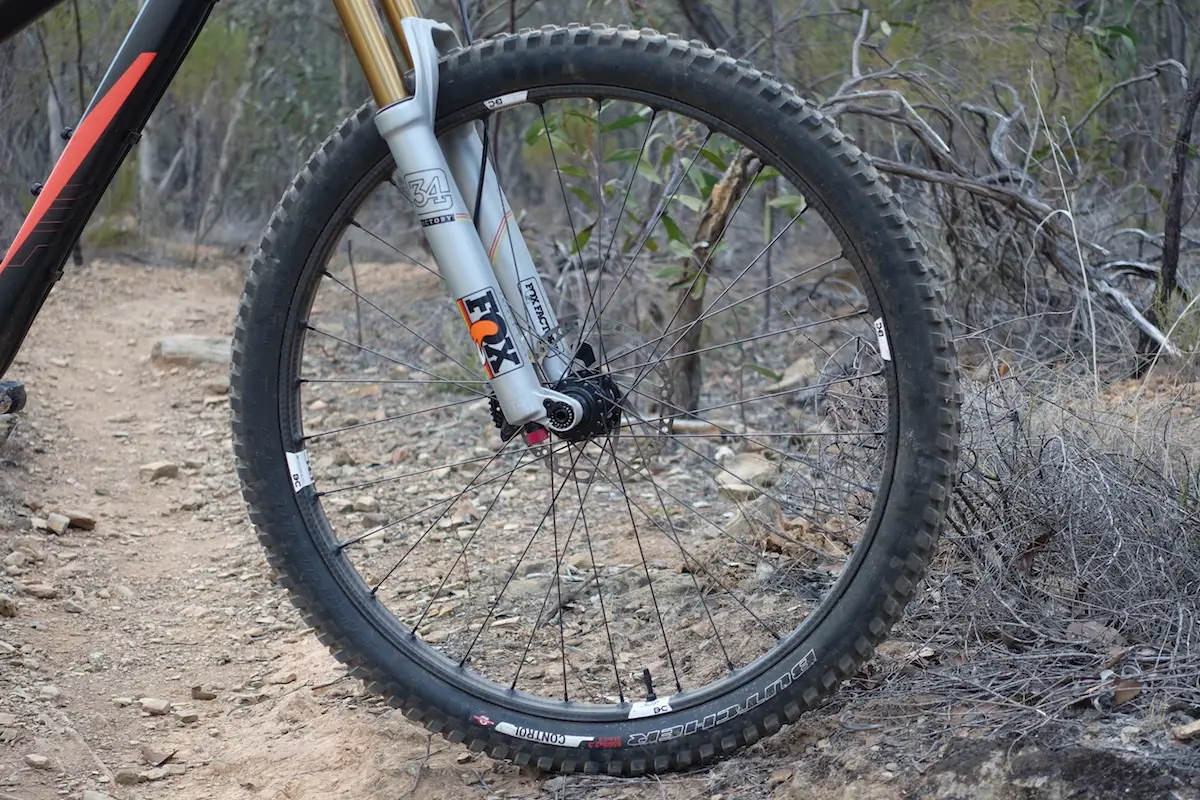
The Tammar rims measure 38mm externally and 31.5mm internally, which puts them at the wider end of the scale. They have a hookless bead and a deep central channel to aid tubeless inflation. With every test tyre I used on the Tammar rim, they all snapped into place at around 20psi, and all with a regular floor pump. Nice.
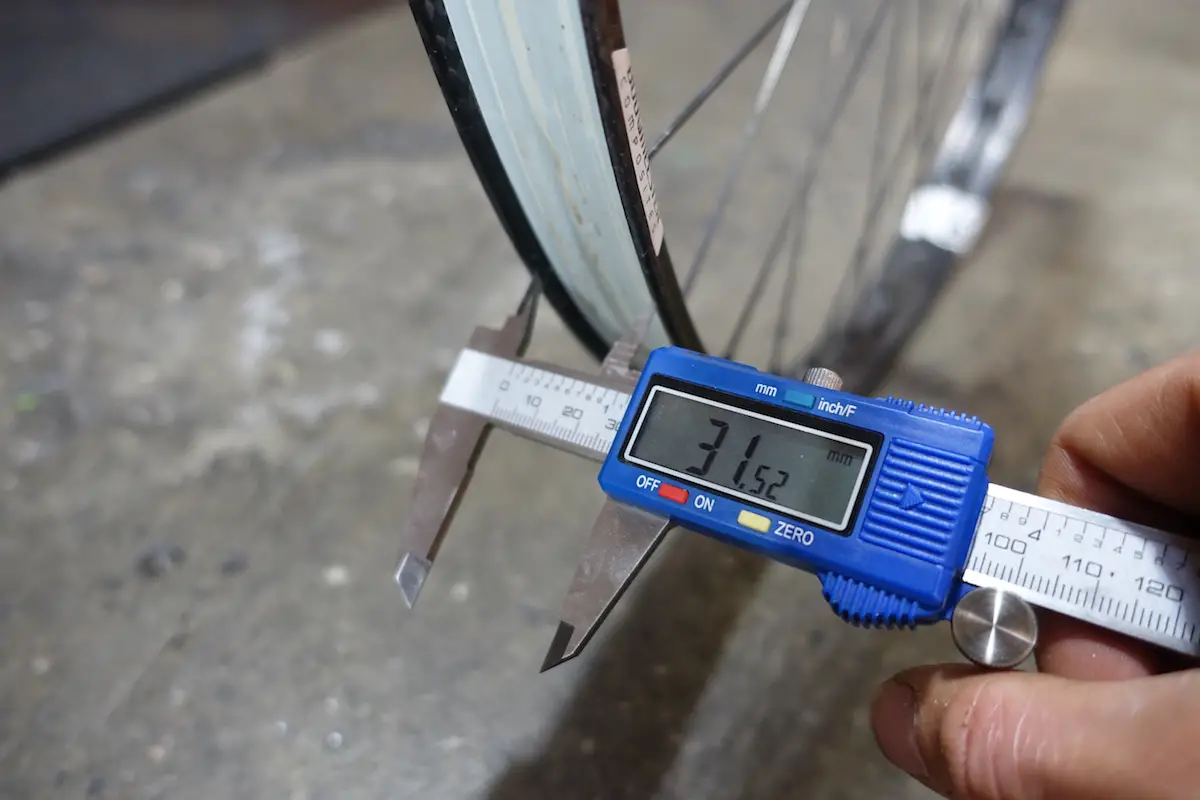
The rims are asymmetric to reduce wheel dish, and they’re front and rear specific to accommodate the different forces transferring through each wheel. The front weighs in at 480 grams, and the rear is 490 grams.
You can get the Tammar wheelset built with DT Swiss 240 or Chris King hubs, though BC also offer a custom service with more hub options should you have something fancier in mind. They’ll only build the wheels with stainless steel DT Swiss Competition spokes though. This is because lighter spokes experience more elongation, and BC aren’t interested in compromising the handling of their wheels.
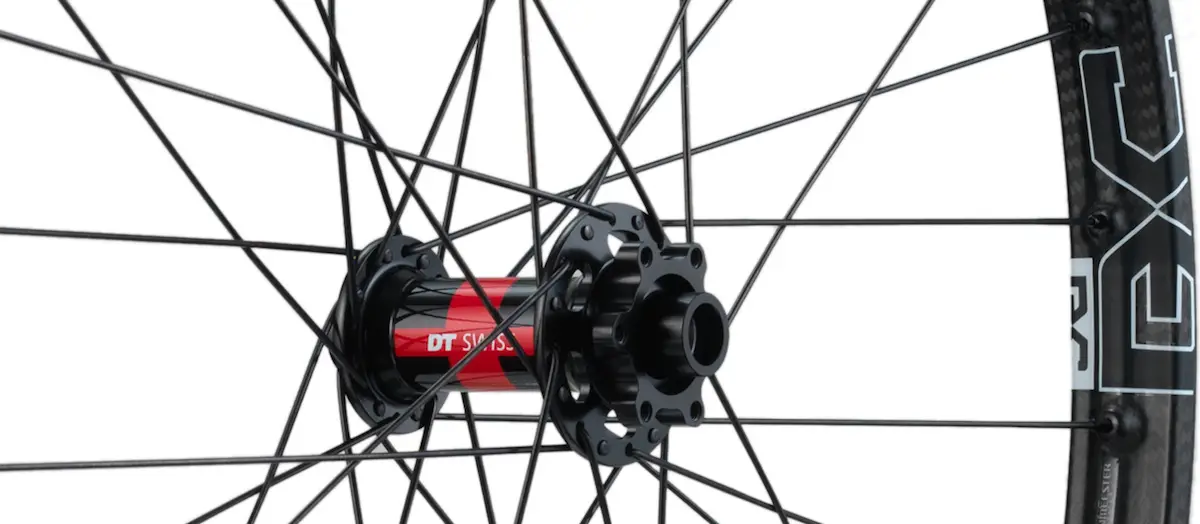
With the Star Ratchet freehub mechanism, sealed cartridge bearings, standard J-bend spokes, and 3-cross lacing pattern, the Tammar wheelset has clearly been designed and built by someone who has spent a lot of time in bicycle workshops.
Functional? Yes. Fancy with proprietary parts? The Tammar wheelset is most definitely not.
Including the provided rim tape and tubeless valves, our test wheelset came out a confirmed 1840 grams. It’s respectable, but definitely weightier than the big-name competition, which includes the SRAM Roam 60 (1625gm), the Reynolds Enduro (1565gm), and the ENVE M70 HV (1679gm).
But while there may be lighter wheels out there, as I would find out, there’s a lot more to the Tammar wheels than just a number on paper.
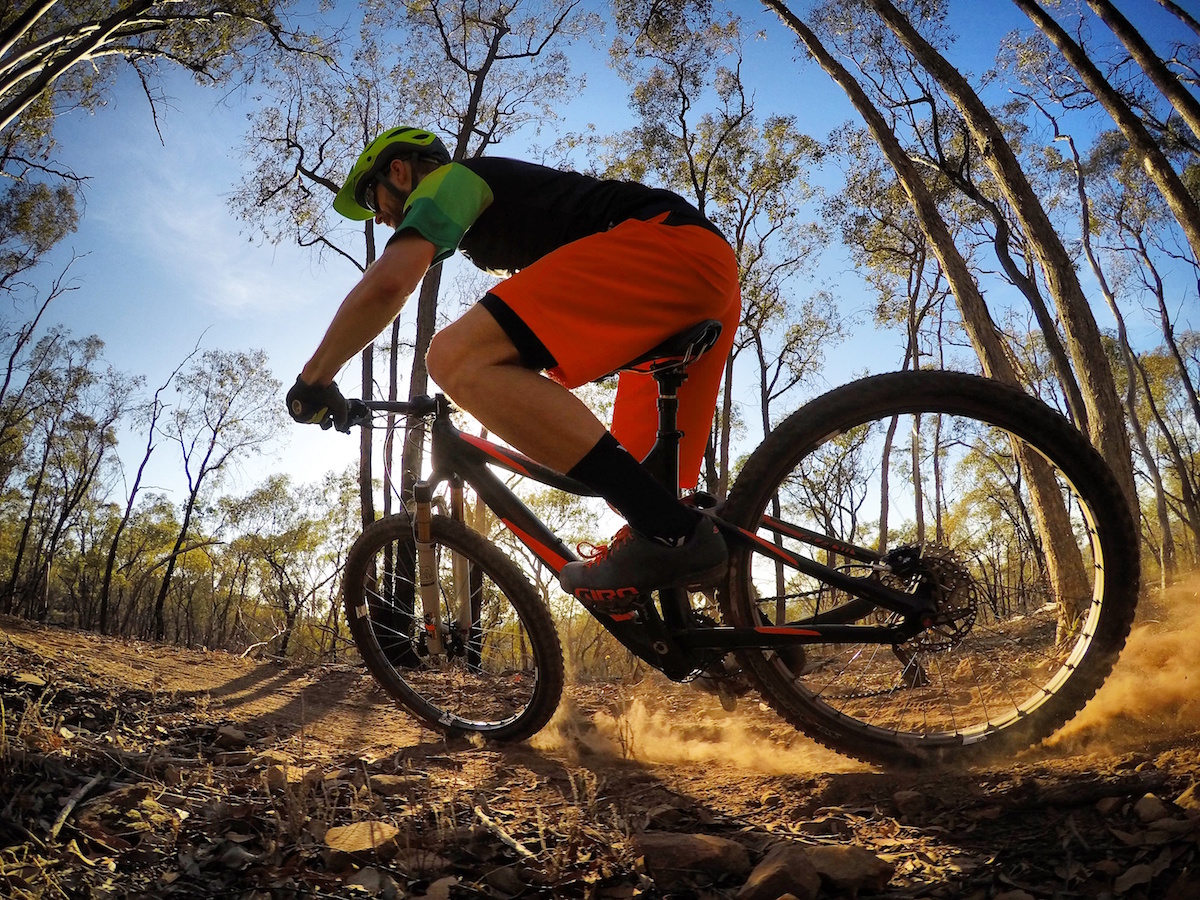
On the trail
The first thing I noticed with the Tammar wheels is just how incredibly smooth they are to ride. They’re also deadly quiet, because unlike a traditional hollow rim, the solid rim construction doesn’t resonate trail chatter. As a result, you simply don’t notice them underneath you.
Crank the pedals a little harder though, and the Tammar’s immediately respond with crisp acceleration that belies their on-paper weight figure. They’re highly reactive to steering inputs and there is little hesitation when you need to quickly change direction on the trail. I put this down to the taut build and the excellent overall wheelset stiffness.
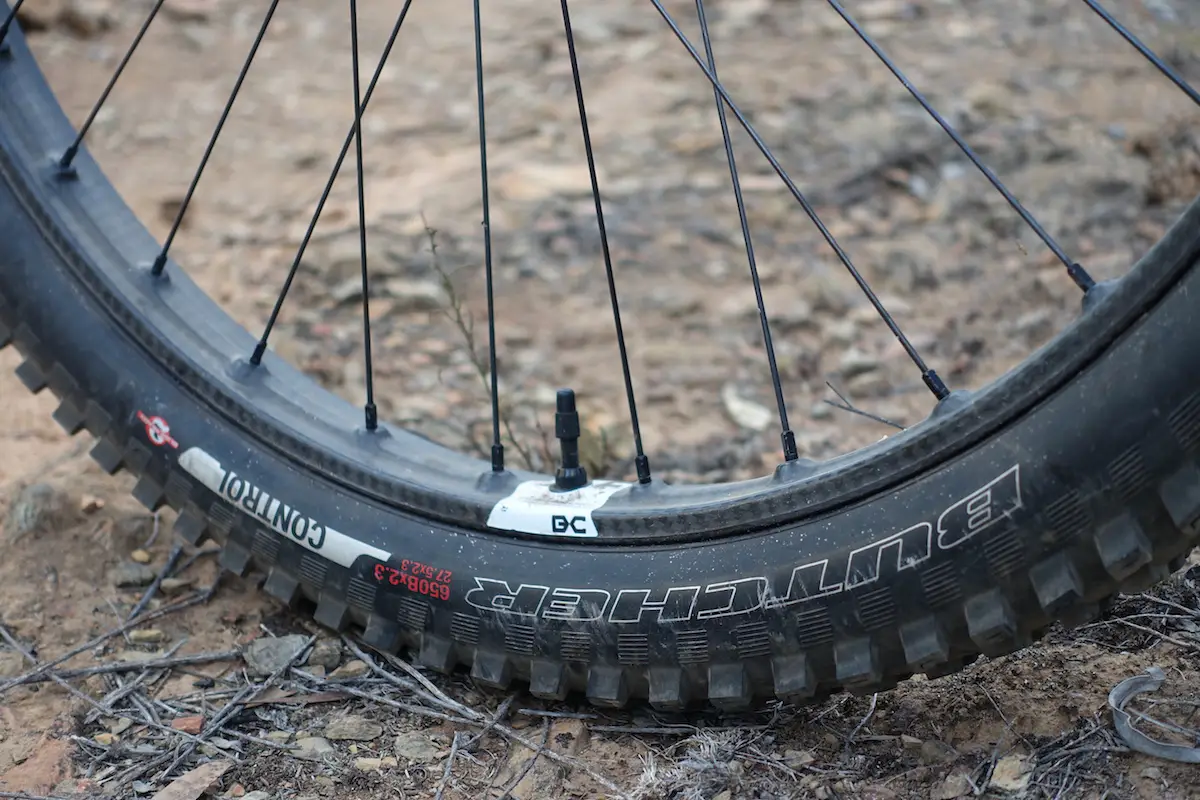
As with other modern wide rims, the generous internal rim width on the Tammar’s helps to add stability to tyres when running lower pressures, though tyre choice is crucial. Not every tyre profile enjoys being stretched out beyond 30mm, but get the right combination, and you’ll enjoy more cornering stability, with less tyre ‘wobble’ through the turns. As an example, the 2.35in Maxxis Ikon I tested on the rear was terrible, since the casing ended up bulging out wider than the tread itself. I had much better luck with Maxxis Minions and the Specialized Butcher/Slaughter combo.
The best attribute of the Tammar wheels though is just how little you get pinballed off of rocks, and especially the ones that you don’t hit head-on. During high-speed entries into an ugly rock garden on my local test loop – the kind that eats tyre sidewalls for breakfast – the Tammar wheels added a whole new level of composure and stability to the bike. When I’d normally be wrestling with the handlebar, all of a sudden I found a greater ability to keep the bike tracking in the direction I wanted it to.
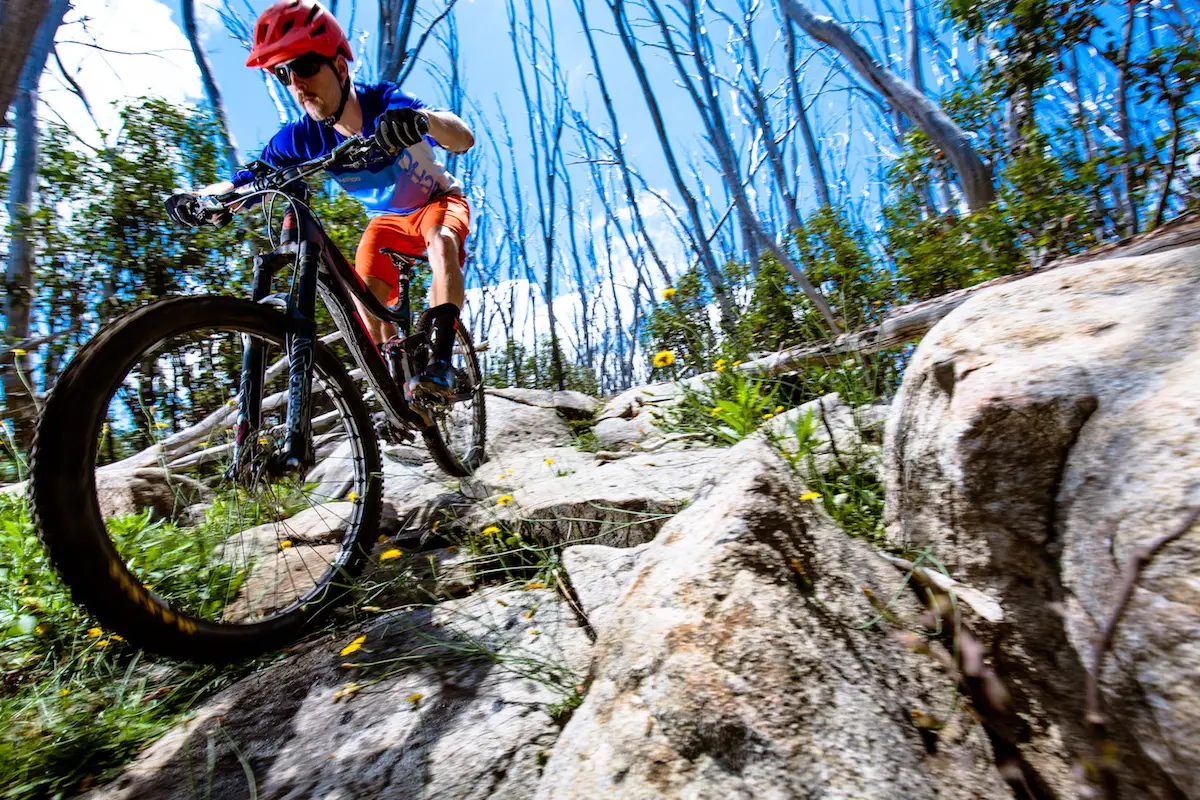
Modern mountain bike chassis’ are by design, very uncompliant. Beefy carbon frames, tapered head tubes, big fork stanchions, thru-axles, and oversized handlebars are all responsible for turning the front-end of our shred-sleds into a surgical tool. Throw a stiff and super-wide carbon wheelset into the same mixing bowl, and you have effectively created a conveyer belt that collects every bit of trail feedback and delivers it straight into your grips. While the marketing taglines have been telling us all along that “stiffer is better”, Bouwmeester ain’t so convinced that’s the case.
The in-built compliance of the Tammar rim is very deliberate on BC’s behalf, and it’s a result of that thick, single-wall carbon rim. While the wheels have plenty of ‘global’ lateral stiffness, the rim is allowed to flex at the tyre contact point. This helps to drive more of the tyre back onto the trail surface for added traction. I can’t say I noticed a dramatic increase in cornering traction with the Tammar wheelset, but what I did notice was a smoother, and more forgiving ride. The fact that I could notice this on a 150mm travel All Mountain bike makes the Tammar’s ride quality all the more impressive.
The best way to summarise their on-trail feel? It’s as if BC have combined the responsiveness of a stiff big-section carbon wheel, with the smooth riding nature of a lightweight alloy rim.
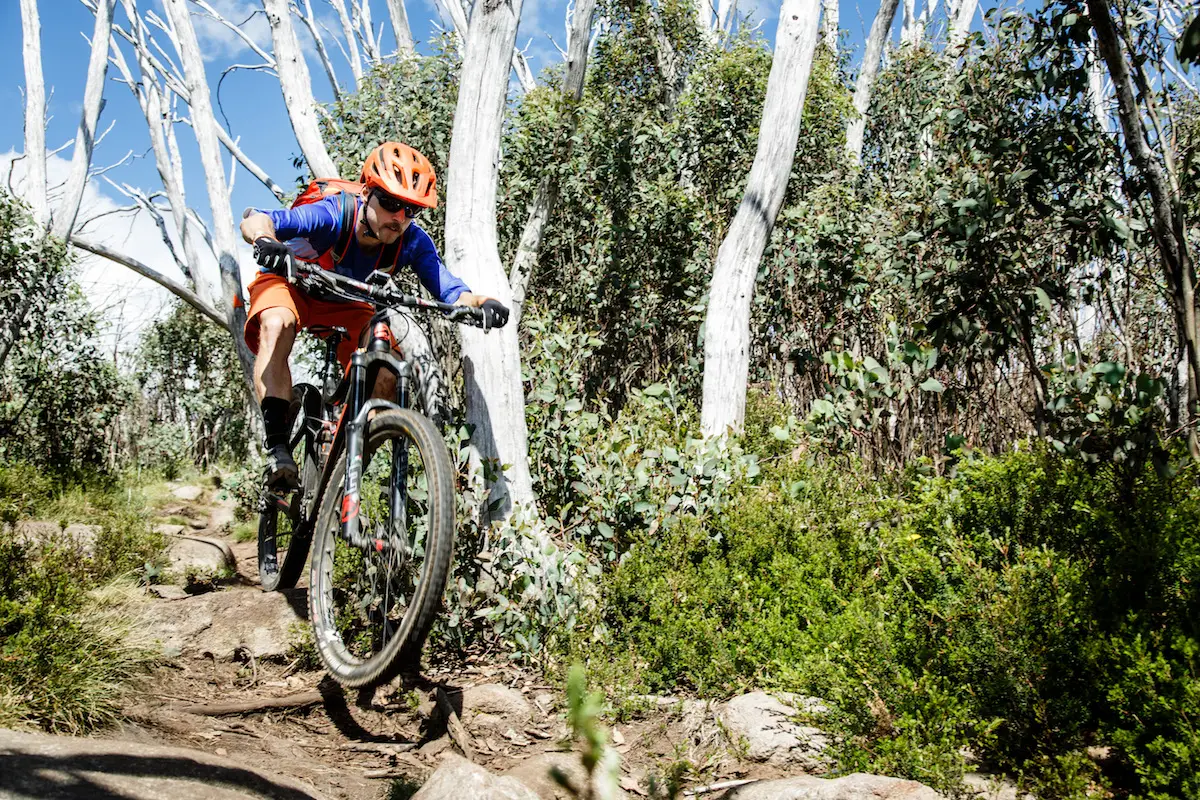
CRASH, BANG, WALLOP!
Throughout the test period, the Tammar wheels have been bulletproof. Halfway through the test period though, I did have a bingle.
With the rear 2.35in Maxxis Ikon setup at a rather low 19psi, I absolutely walloped the rear wheel into a sharp imbedded rock on a heavy, and very inelegant landing. There was a loud “CLUNK”, my arse puckered, then when I realised I hadn’t flatted, I continued riding and completely forgot about the incident.
Over the following couple of weeks, I noticed some light pressure loss from the rear tyre. Nothing drastic, but a couple of psi would leak out overnight. Whilst I was loading my bike onto the roof racks of our shuttle car during some downhill runs at Mount Buller, I discovered the source of the leak: a tiny fracture on the rear rim. Clearly my awkward landing from a few weeks ago had left its mark.
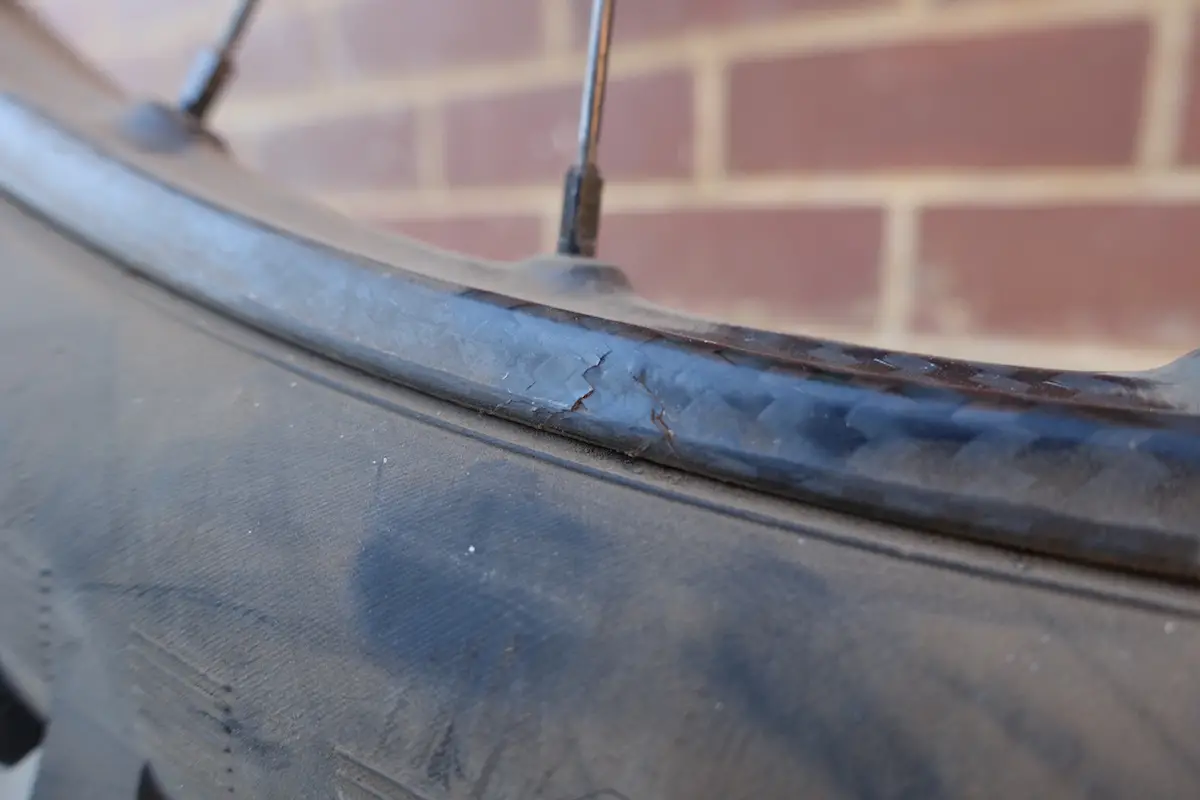
After speaking with Mello, I sent back the wheel to have the rear rim assessed. It turns out there were actually two small fractures in the same position, which indicated that the wheel had copped two separate impacts. Here is Mello’s response:
“Yes, we’ve closely examined the rim in the lab and analysed it using a few methods. I’m not going to give the standard ‘it was a pre-production rim’ line, as we believe in our products and when something happens for the first time it deserves a valid response. Basically there are two small localised delamination areas in close proximity in the rim wall, which is in line with being caused by multiple impacts. The energy that it would have taken to cause this damage is considerable, and we know from our rigorous impact testing program this energy would have likely folded an aluminium rim wall, or caused major delamination to the majority of other carbon rims making them un-rideable. Basically, you certainly wouldn’t have finished your ride or race on another product.”
Embarrassingly (or impressively, depending on how you look at it), this was the first Tammar rim in existence that had been cracked outside of the lab. It just happened to occur while I was the pilot. One thing worth mentioning that Mello informed me during our conversation about the rim crack, is that our test wheelset had already been in circulation for over 12 months under various reviewers from all over the world. Given it’s history, who knows what kind of torture and km’s our Tammar wheelset had already been subjected to.
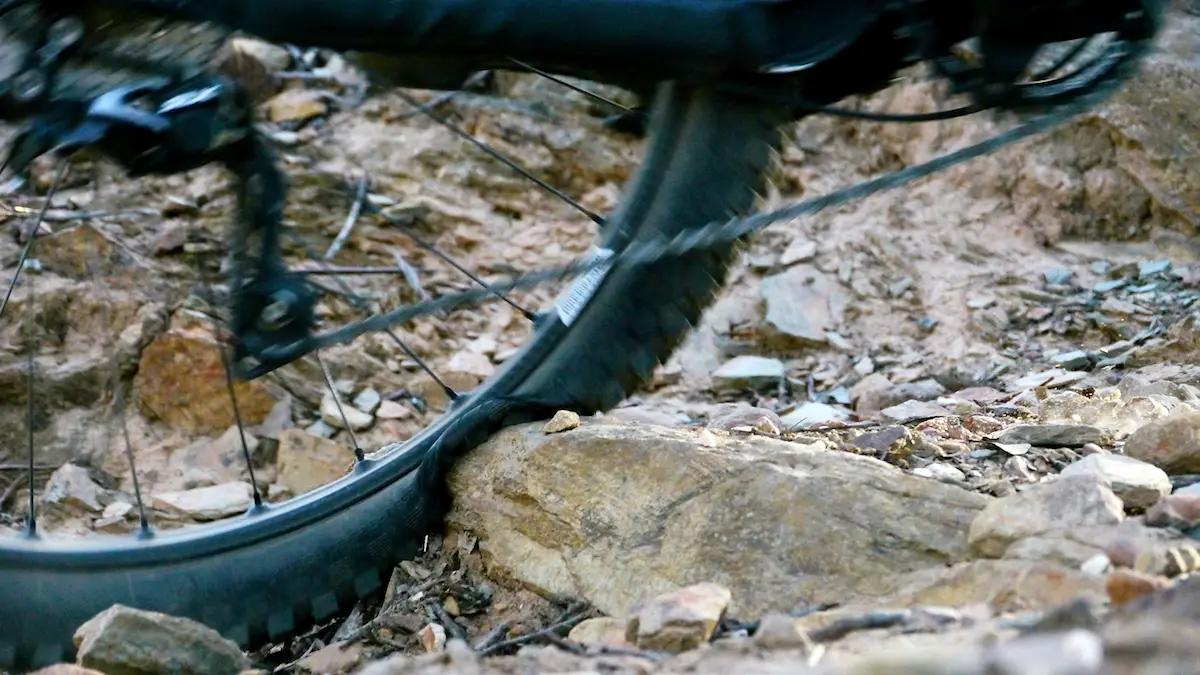
What was most impressive about this experience though was the fact that the wheel was back in my hands within a week, with a brand new rim. BC’s guarantee is that if you break a rim in the first 12 months of ownership, they’ll replace it free of charge, no questions asked. Frankly, that’s incredible. Following that, their rims come with a 3-year warranty against manufacturing defects, such is the confidence they have to stand behind their product.
Was I pissed off about the crack? Not really, because shit happens, and on mountain bikes, shit breaks. Assuming that wheels can’t break is like assuming your carbon down tube is invincible to rock strikes. In actual fact, I was actually a little bit smug that I managed to the only person who has thus far broken a Tammar rim. Ultimately it came down to rider error and it was a huge impact. The fact that I continued riding for two weeks afterwards without incident is a testament to the rims overall strength and build quality.
Would I still recommend the Tammar wheels? Absolutely. With a high-end product like this, for me it comes down to after-sales service, and in that sense, BC appears to have it nailed.
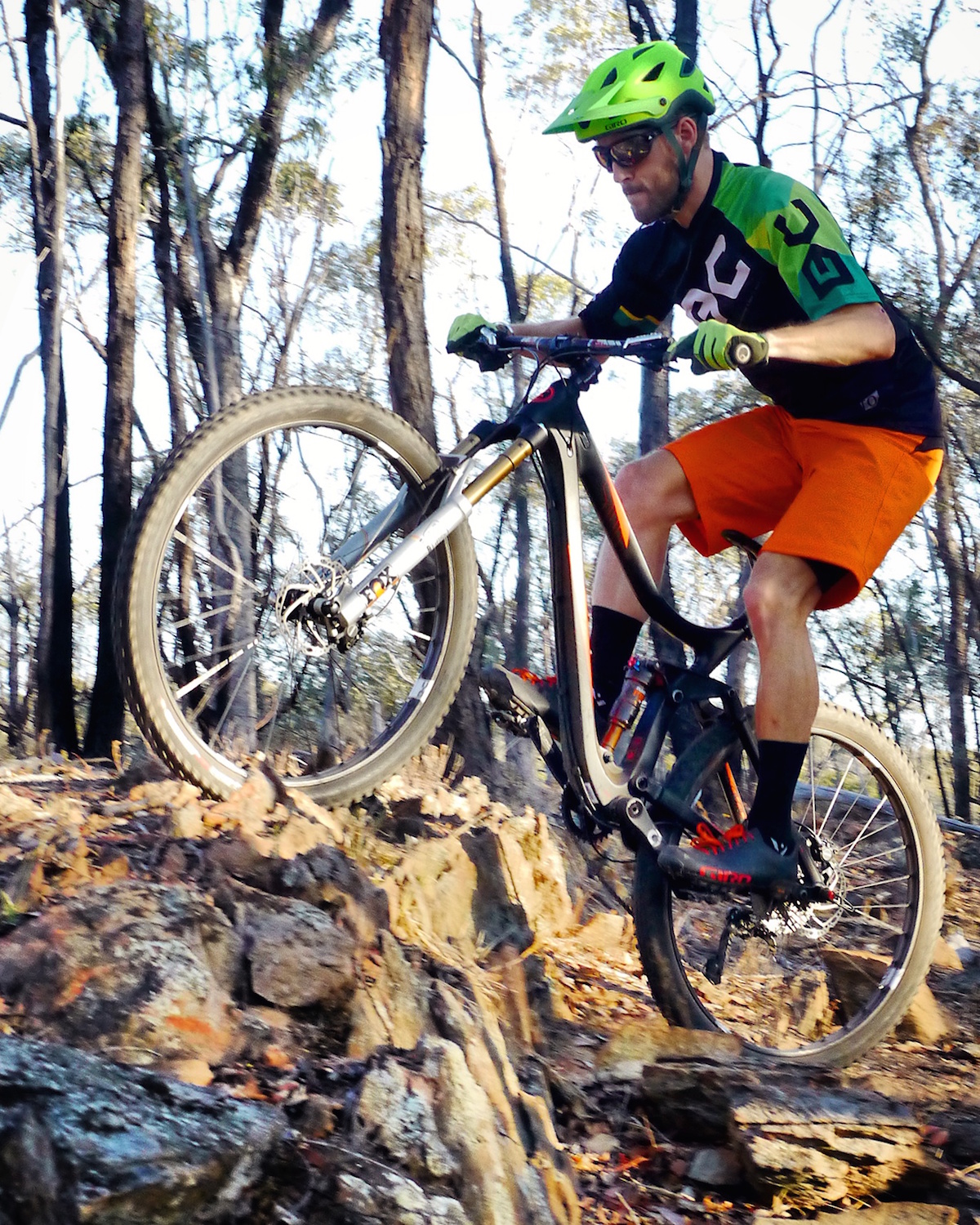
Overall
At $3499 AUD (about £2000 at the time of writing), the Tammar wheelset is an expensive upgrade for any mountain bike. That said, they’re hands-down the best riding 27.5in trail wheelset I’ve ever ridden. They deliver an incredibly smooth ride on the trail, combining handling precision with in-built compliance like nothing else I’ve ridden before. Factor in the Tammar’s unique design, their brilliant on-trail performance and the fact that they’re handmade and handbuilt in Australia, and I believe they’re worth every dollar. My direct experience with their after-sales service only cements that opinion.
Relative to the competition, the Tammar wheelset comes in around the same price as an equivalent Reynolds, SRAM or Shimano wheelset, and they’re actually cheaper than an ENVE wheelset. I know what I’d be buying.
Currently there is no distribution for Bouwmeester Composites in the UK, though wheels are available for direct purchase from Australia through BC. For further information about the Tammar wheels, head to www.bouwmeester.com.au for all the details.
Review Info
Brand: | Bouwmeester Composites |
Product: | Tammar V4.8 |
From: | www.bouwmeester.com.au |
Price: | £2000 |
Tested: | by Wil Barrett for six months |