Ever wondered how Continental tyres get made? Or indeed how any tyre is made? We sent our man James Vincent to have a look behind the curtain at the Continental tyre factory, Korbach, Germany.
I’ll tip my hat to the new constitution
Take a bow for the new revolution
Smile and grin at the change all around
Pick up my guitar and play
Just like yesterday
Then I’ll get on my knees and pray
We don’t get fooled again
No, no!
The naming of the tyres
David (Vollmer, Sales Manager), warned me about this at the beginning of the day. In fact, in the most Teutonic of ways, it was on the schedule. 12.00pm Lunch, 14.00 Feedback.
We’ll gloss over the fact that we were late thanks to a detour to the best coffee machine in the factory (it’s on the same floor as the R&D department in case you ever find yourself at a loose end), but yes. Feedback. A chance for Continental to grill me and get my opinions on the important matters of the day: Yes, Brexit is a total shitshow. Yes, I think the new Athertons’ bike looks awesome. And no, 8am is not an appropriate time to be drinking beer, even if you are in an airport! Oh, not those kind of opinions. Sorry, where were we…?
“Do we change the name of the tyre?” David asks. “Huh!? Why would you do that?” I query.
“The new Baron is a completely different tyre” he replies. “Yeah, but that’s just going to confuse people,” counters Rob (Scullion, Sales Manager at Cambrian Tyres) – “it’s got the same intended purpose, the studs are similar. You can’t change the name, you just can’t. It’ll be a marketing nightmare.” He’s got a point, and I agree – it’d be chaos. But apparently it’s a hot topic in Korbach at the moment, with two camps taking opposing sides. Even though they look very similar (the untrained eye would struggle to make out the differences), every aspect of the tyre, casing, tread pattern and graphics, is brand new so I can just about understand why you’d want to change the name. Make a fresh start and all that. But then again, from a marketing point of view, chaos.
Baron Ron Ron Ron, Baron Ron Ron
But we’re getting ahead of ourselves here – let’s back up a bit first. I mean, a tyre’s a tyre, right? What difference does it make if it’s handmade in France, Germany or wherever? Machines do this sort of stuff way better. And anyway, we’ve been through all this already a couple of years ago with Hutchinson. Take a woven carcass, some fancy rubber, and a bead of some description, wrap it up in the latest tread pattern de jour and get it put together by a machine somewhere deep in the far east (I know, such a cliché).
Deutsche Technik
Erm, it seems like someone forgot to tell this to the guys at Continental, who’ve been making a big deal out of their handmade in Germany tag for quite a while now. Some of you may remember their successful “Deutsche Technik” ad campaign from a few years back, featuring bearded factory worker Ulf Gunzel as the friendly, human face of a large corporate monolith. Continental want you to know that these are premium tyres, put together by hand, in the small town of Korbach, a couple of hours drive north of Frankfurt, Germany.
Pulling off the autobahn and driving in to Korbach, one of the first things you see is the Continental tower, rising up and dominating the skyline, just as Continental dominates the town. With a population of roughly 32,000 people, more than 10% work at the sprawling Continental factory, producing all manner of tyres – car tyres, van tyres, tyres for industrial applications (think fork-lift trucks etc) and hose. Thousands and thousands of metres of hose (185,000 metres per day to be precise!). And no, I don’t mean garden hose. I’m talking high tech hose for car brake lines and other safety critical industrial applications.
Sing Hose Anna
But dear reader, I didn’t come all this way to look at hose. Within the Singletrack team I seem to have developed a certain niché as the go to guy for tyre reviews and factory visits, so I’m here to check out a teeny tiny corner of the vast 347km2 site that’s dedicated to manufacturing Continental’s ‘Best’ range of road and mountain bike tyres. Sure, others may get whisked off to exotic locations to ride top secret bikes down dusty trails, but that doesn’t bother me (too much). I’m going to embrace the role I’ve been given and go ogle some rubber.
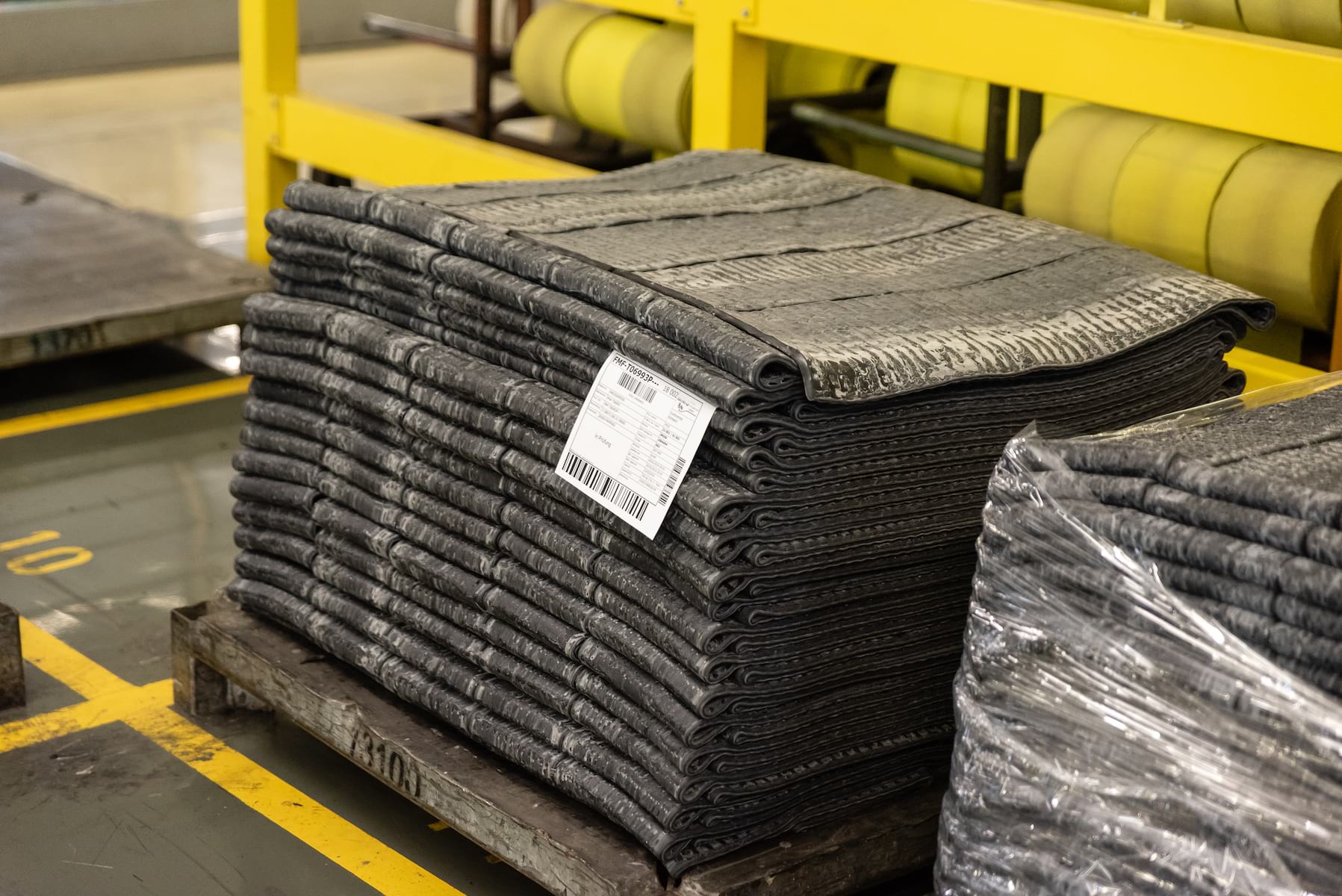
The same, but different
I’ve been invited out to Continental at a pivotal point in their MTB tyre history. A change of management has led to a complete refresh of their MTB portfolio all the way from the XC race orientated Speed King, right up to the downhill focussed Der Baron. Previous wisdom decreed that if a tyre was big, heavy and covered in enough studs it would be ok. The fact that it weighed a ton and the compound wasn’t up to scratch was largely irrelevant as it looked right, and that’s all you needed from a downhill tyre. Nowadays, all the designers and product managers here are keen riders, and Continental continues to draw heavily on the knowledge imparted by their impressive roster of sponsored athletes and brand ambassadors. Danny Macaskill, Fabio Wibmer and Andreu Lacondeguy all take an active role in the development of new tread patterns and tyre design, while the compounds are worked on in secret by the might of the R&D facility in Hanover.
Selecting the deep cuts
Rob is also particularly excited to welcome The Athertons™ back into the family as he grew up racing with them, and the Cambrian Tyres HQ is just down the road from Dyfi Bike Park in mid Wales. He takes delight in telling me how much they (The Athertons) love the Mud King, how versatile it can be with three specific stud cutting levels (box fresh, one cut, and then a second deeper cut for minimum rolling resistance), and that this is the tyre Gee won the infamously sticky and pedally 2014 Cairns World Cup race on after switching to flat pedals and a pair of Five Tens borrowed from a trackside spectator.
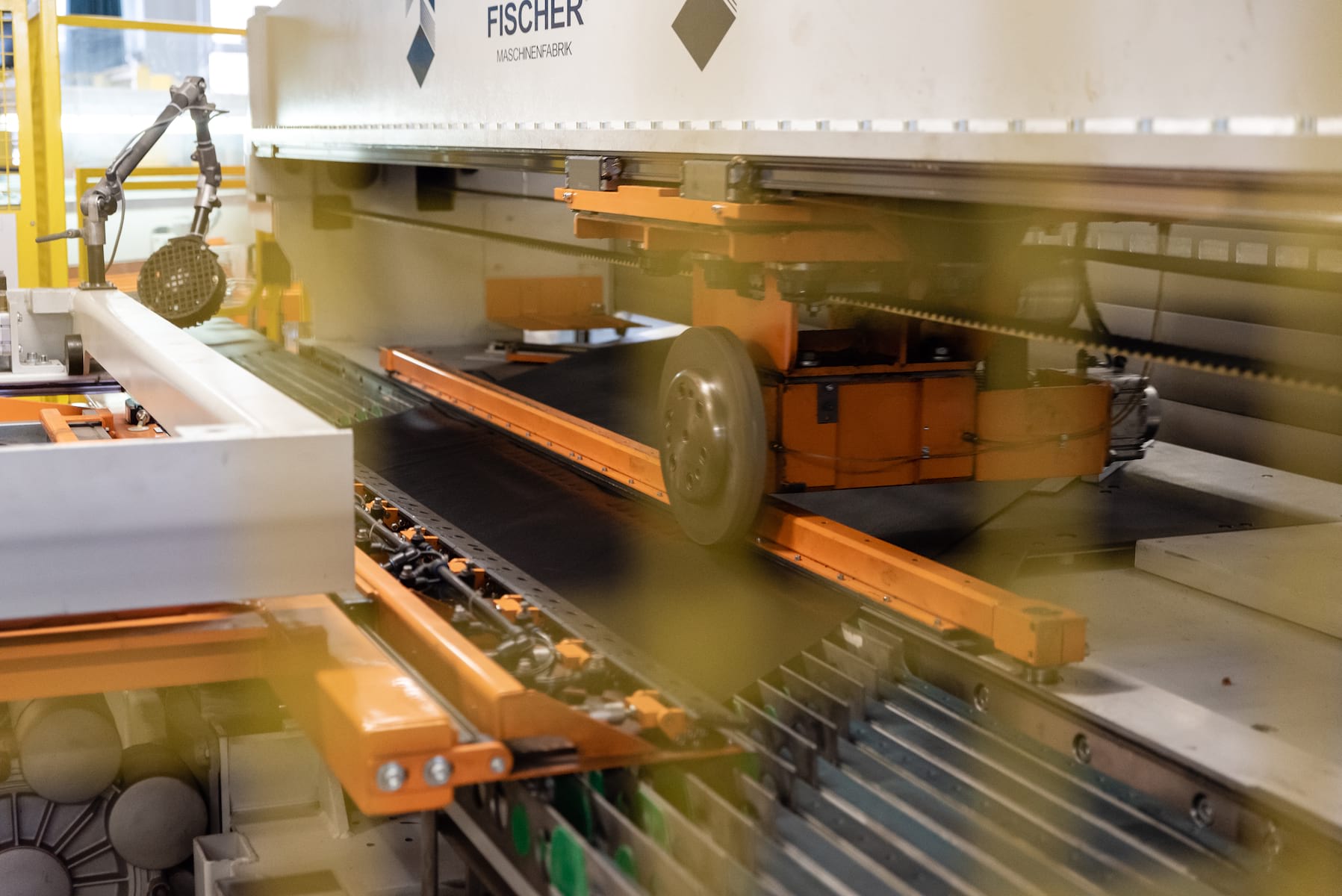
Der Volksreifen
Back to the revamped range, and the names remain the same but under the skin everything else is new. Across the board there are new compounds, casings and tread patterns, and the graphics have been tweaked too. This last is an inconsequential update from a pure performance point of view, but it helps place the tyre within the bigger picture.
Continental make its bike tyres in three factories across the world – India, China, and Germany, and the ranges reflect this – Good, Better, and Best. The names and tread patterns are the same throughout so you’re still buying into the same family – think of it like buying a VW Golf – you can buy the base model and still have a Golf, or you can drive away in an all singing, all dancing Golf R with all the performance benefits of the premium product.
The best range is handmade in Germany, features the BlackChili compound, Apex sidewall protection and is designed for experts, athletes and those who simply must have the best of the best. Dropping down to the tyres made in China, you get the PureGrip compound, and the range is intended for weekend warriors and those on more of a budget. You lose the Apex sidewall protection, but it’s still a tubeless ready tyre and at a much keener price point.
Finally, you have the tyres made in India, which are an entry level option, and generally OE specification with a wire bead.
The BlackChili Source
In today’s numbers driven marketplace where every aspect of a bikes components can be stuck on a spreadsheet and quantified, Continental buck the trend and offer up no data on their legendary BlackChili compound. Unlike the majority of their competitors, you’ll see no mention of durometer ratings for their tyres to set them apart, although to be fair, this isn’t them being obtuse for the sake of it. The base ingredients that make up their BlackChili compound are so finely ground and the resulting rubber so dense, that apparently it can’t be measured the same way as regular rubber and thus the durometer readings would be all wrong anyway. Likewise, in a world full of pick ’n’ mix casing choices, you’ll get none.
Continental believe the performance of a compound and carcass are so interwoven and have such a dramatic impact on the ride quality of a tyre that they display a refreshing confidence and make the decisions for you. Too much choice can be a dangerous thing and by matching the wrong carcass with the wrong compound you could end up with a compromised product, not to mention a bewildering range of tyres.
Think about it – 2 wheel diameters, 2 casings and 2 compounds makes for 8 different tyres already. Throw plus sizes and fat tyres in to the mix, and you’ve increased your range exponentially – before long, you’re looking at a vast product matrix that’s impossible for a bike shop to maintain comprehensive stock of. These Germans could be onto something you know…
More Chili Jam
When it comes to developing and manufacturing compounds, the importance of being on the same site as the car division is not to be overlooked. A certain US tyre manufacturer head hunted the designer of the BlackChili compounds, only to discover that without certain prohibitively expensive machinery, the BlackChili compound is impossible to recreate. And when BlackChili is referenced by another manufacturer in their marketing materials, you know Continental must be doing something right.
Talking of which, less than a week after my Continental factory visit, I found myself in the Middle East documenting Team GB ultra runners Robbie Britton and Dan Lawson as they ran the 650km length of the Jordan Trail in under 10 days, and I spot a well used pair of Adidas trainers in a pile of kit. They’re shod with Continental rubber so I’m immediately drawn to them, and both runners start eulogising that the Continental grip is the best on the market. “You think it’s a gimmick, but then you wear them in the wet and it’s like, bloody hell! The grip is brilliant. They’re great!”
Can’t argue with that now, can you?
Design of the times
Leaving the briefing room, the first office we stick our noses into is home to the designers, Benjamin Reuter and Oliver Martinez. Alex (Hänke, MTB Product Manager) runs off to find out what tyres are in production today, and as if it had all been planned in advance, returns moments later to inform me that we’ll get to see The Baron from start to finish. Ben duly pulls the 3d model up on screen and I get to explore the intricacies of a very complex rendering. It’s pretty hard to visualise, so he shows me a 3D printed model of a cross section of tyre. This is produced up on the top floor in the R&D department, and is an invaluable tool in the development of new tread patterns.
Unfortunately, the next stage of manufacture is out of bounds to my prying camera lens. Rob is incredulous that Hutchinson let us see their mixing process, let alone see the raw materials and take photos. Calendaring is also out of bounds, but only due to planned maintenance and construction – it would appear that there are only so many ways that you can coat a piece of fabric with rubber, so I don’t think I’m missing out on any trade secrets.
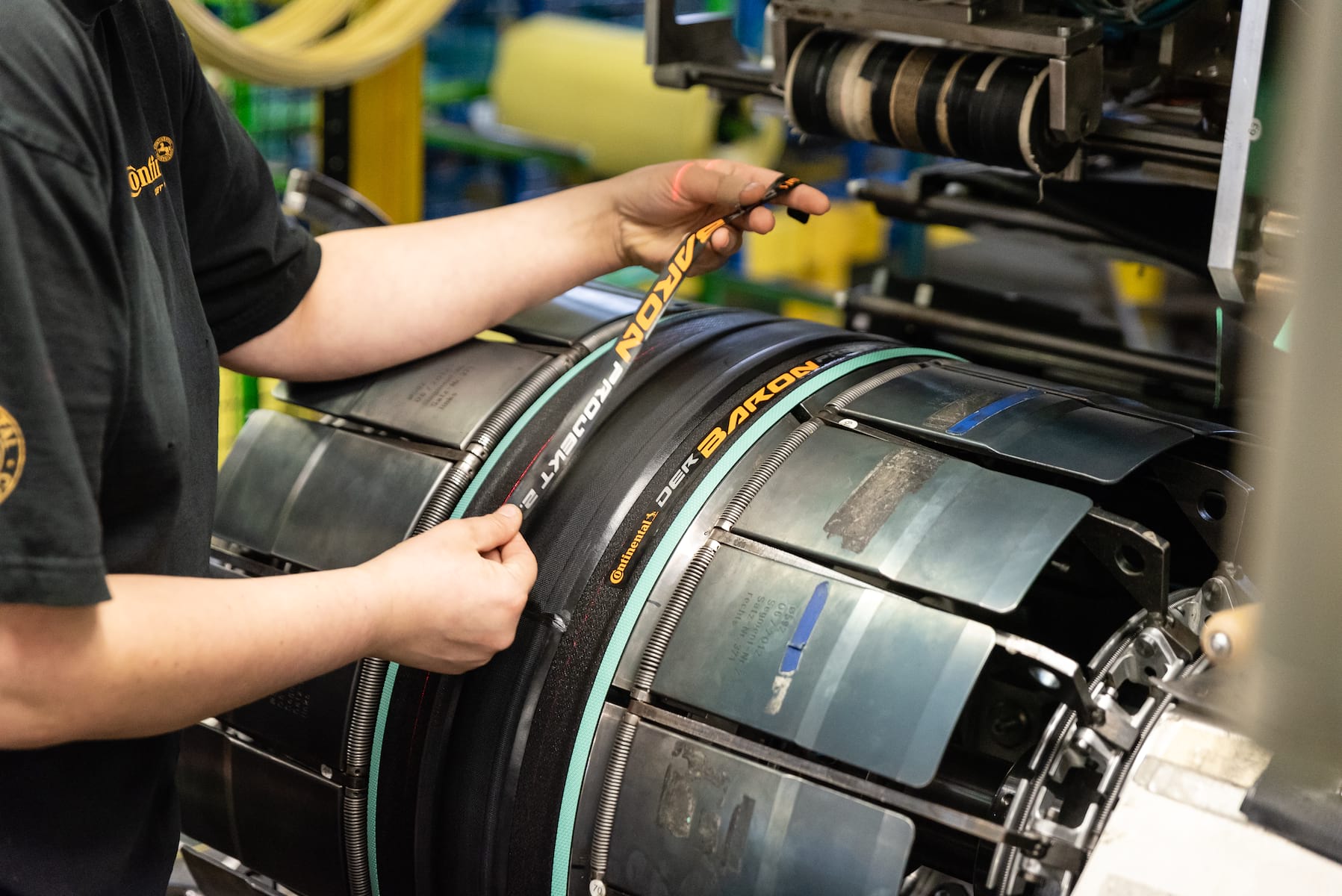
Go Compare
As we move further into the factory, I’m struck by how familiar everything is, and yet how subtly different it all is from my visit to Hutchinson a few years ago. And it’s not just the layout of the factory – while Hutchinson was contained all on one floor and the tyre construction reflected this, the Continental factory is spread over multiple floors. Hutchinson run long strands of Kevlar bead throughout the factory, threading from one station to the next, while Continental finish their beads into preformed rings before wheeling them on racks to the next station. Likewise, when it comes to cutting the carcass, Hutchinson change the angle of the blade, while Continental prefer to have a huge stationary blade and change the angle of the carcass being fed into it.
Ignorance is amiss
My (little bit of) prior knowledge comes in handy, and we can gloss over the basics of tyre construction and dive into things in more detail, such as how the angle of the carcass thread changes the characteristics of a tyre. A steeper angle (roughly 60°) makes for a faster tyre, while a shallower angle (40°) adds flexibility and compliance. Road tyres tend towards a steeper angle, while naturally MTB tyres go for a shallower angle and greater comfort.
There’s a relaxed atmosphere everywhere we go, and it’s not just that Friday feeling. It’s properly busy – a few years ago there used to be one 8 hour shift per day, but to keep up with demand, the Continental factory now runs 24/7 with three 8 hour shifts. There’s a definite air of efficiency, where everyone knows their job and gets on with it, but that’s not to say it’s a soulless place. Far from it – the canteen at lunchtime is convivial and welcoming, and when we detour to the famed coffee machine, Rob knows everyone and chats away like catching up with long lost friends.
Come together
Back on the factory floor, and we find ourselves at row upon row of stations where the individual components (carcass, protection, beads, tread and labels) come together. From this point the raw tyres are moved on to banks of steam powered curing stations, where the sulphur bridge bonding takes place.
The tyres are placed on a drum, and a balloon inflates with steam, forcing the casing into the mould for a few minutes, turning the soft, sticky rubber rings into a recognisable and finished tyre. It’s like a scene from Universal Soldier, the machines creaking open in sequence signalled with blasts of steam, and out pops a fresh, steaming Baron ready for inspection, packaging and distribution.
This article was produced in association with Continental Tyres
Comments (2)
Comments Closed
Love my Barons but with the new version have they done anything to improve the sidewalls? Threads wear through so quickly.
Regarding the name change, how would we tell the difference between an old and new Baron in a shop?