I’ve never done this but this is my guess based on my experience and knowledge of the theory. All the hail the internet! 😉
This is a standard wheel viewed from the drive side.
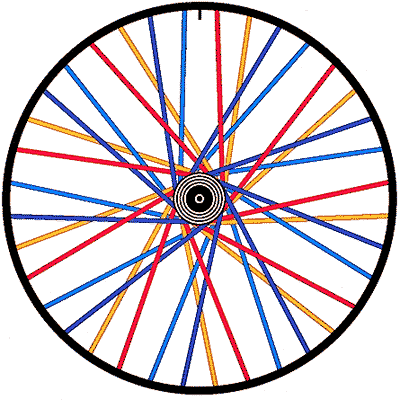
If the hub flanges are not central on the axle then the drive side should be as above but the non-drive side will be rotated anti-clockwise so the yellow/red and blue/blue spokes hit the rim at the same point. This means the yellow spokes will be longer and the blue shorter on the non-drive side. Which would mean 2 different spoke lengths on the non-drive side.
If the hub flanges are central on the axle then it’s possibly best to split the difference so the drive side rotates clockwise a bit and the non-drive side anti-clockwise from the ‘norm’. This should mean 2 different spoke lengths on each side of the hub but they should be the same each side (I think!).
Why this won’t work:
1) With 2 different spoke lengths on the same side of the hub, can you get the tension right?
2) Depending on the distance of the spoke hole from the edge of the flange/angle of spoke out of the hole and then bent over the flange – there may be too much flange in the way when you rotate the hub for some of the spokes to easily exit the outer hole and reach the rim. The large rim width helps you here though.
C’mon STW pull that apart. 🙂
Another option, lace the non-drive side 2 cross? Would this help matters or improve it? (my brain can’t visualise that)
I’m not suprised your wheelbuilder said no, this would melt anyones brain for correct spoke length before you even got near actually building it!