We’ve had 3D printed bikes, and 3D printed components, but these Radic Performance callipers are the first 3D printed disc brakes we’ve seen.
Spotted at Crankworx Rotorua, these 3D printed brake callipers are designed and manufactured in New Zealand by Radic Performance.
Radic Performance is run by Taylor Grey and Jake Powell, 2 mechanical engineers with a passion for mountain biking. With their expertise and skills, the duo saw a way to use an additive manufacturing process to manufacture ultra-lightweight disc callipers.
Additive manufacturing is the same type of process that Robot, now Atherton Bikes, uses for its titanium lugged custom frames. While it might not strictly be the same as 3D printing, the process is similar enough that many brands simplify it as 3D printing for marketing purposes.
Radic Performance is using this high-tech manufacturing process to create the Gamma Disc Calliper, a sub 60g 4 piston calliper that can be used with any brake lever that has a master cylinder of at least 10mm.
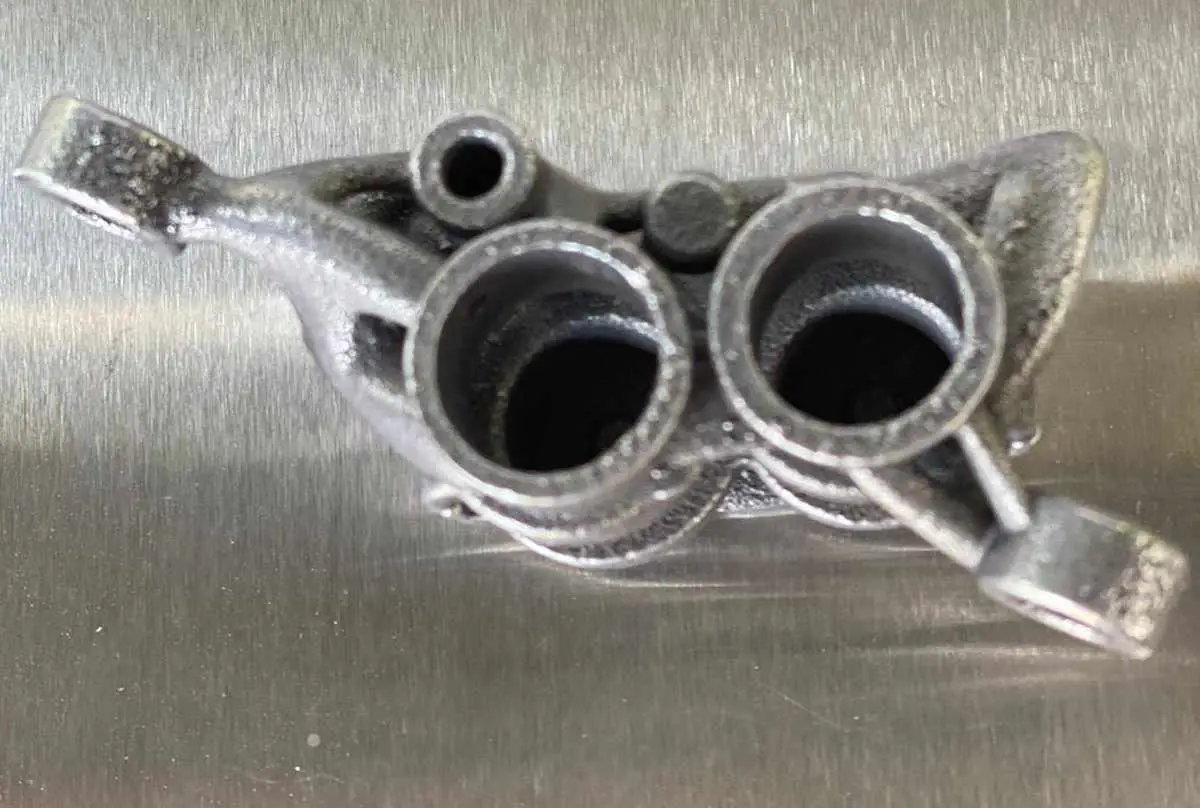
The Gamma’s quad piston design uses 16mm and 15mm pistons for exceptional performance, while heat management is handled through a large surface area design and air cooling vents that run through the body.
On top of being extremely light-weight, the Gamma also promises to be easy to bleed thanks to an oil flow design that is less prone to trapping air. The bleed nipple is also moved out of the way to help prevent accidental contamination of components too.
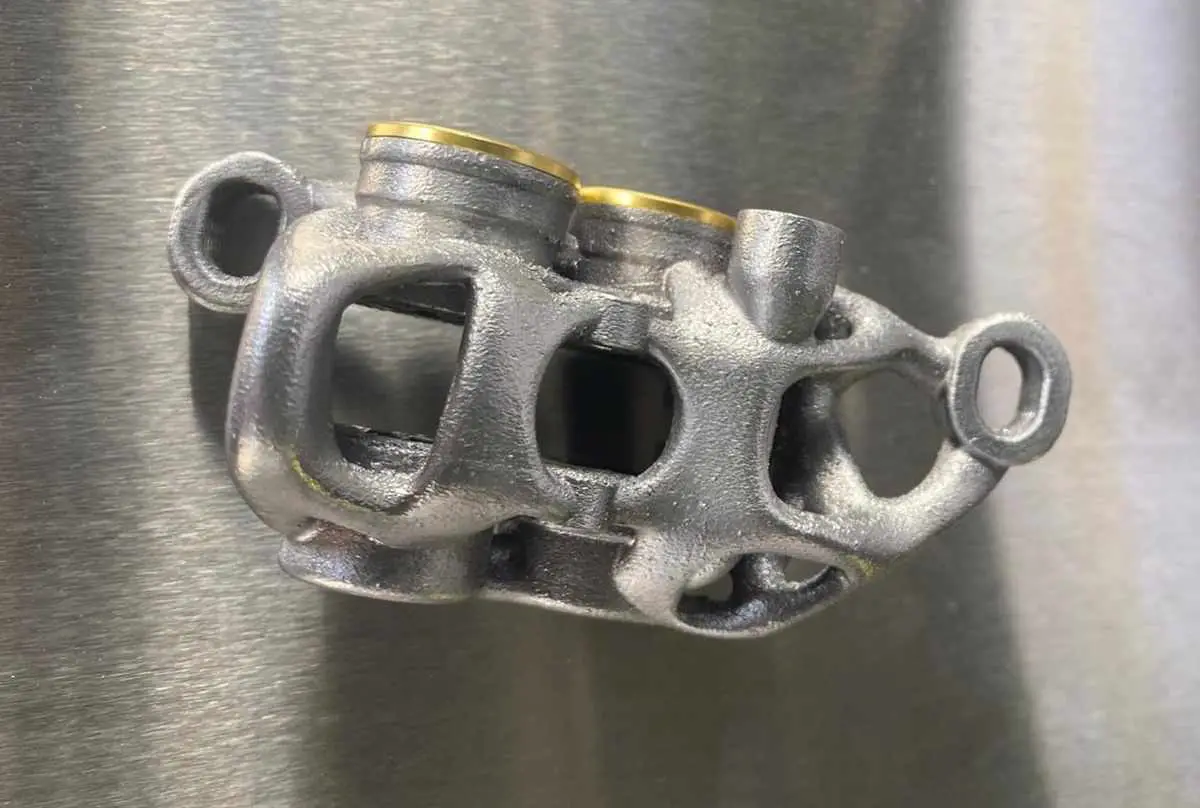
The Gamma has been designed for use with Hope V4 brake pads, so you shouldn’t have any issue finding spares, and you can either spec the calliper with DOT 5.1 or Mineral oil compatible seals, depending on the lever you choose to use.
Radic Performance has all the details of the Gamma available over on their website, and it looks like they’ll soon be offering preorders on this innovative new brake system, however, pricing has yet to be listed.
Comments (5)
Comments Closed
Always interesting to see what can be done, but personally brake calipers aren’t something I want to save weight on! 😉
These 3D printed dis callipers have stupidly small pistons! So you either have to choose between pairing them to small MCs or have poor overall strength with short throw. The mechanical advantage/power of a disc brake comes from the ratio between the master/slave piston areas.
the pistons are the same, or larger than most other popular 4 pot brakes.
We did this for a Mini back in 2011. Scanned the original, topology optimised it, did a proper design extraction (not like the above), printed (titanium), post machined and tested it. Worked fine and still does, but cost about £10000 in time, material and machine cost.
When you can buy 300g of aluminium for £5 and machine it down to 70g for a further £10, why would you AM it at a cost of £60-£100 and still have to machine it at a cost of £10?
I’m all up for using new technology, but as ideas go, this one’s right up there with fairy wings on a cement truck.
“I’m all up for using new technology, but as ideas go, this one’s right up there with fairy wings on a cement truck.”
My new favourite phrase 🙂