jonm – pretty much what you describe. Apologies to others about digressing into framebuild geekery….
Big block of birch plywood laminated together. Each piece of plywood was cut to a slightly different radius so I had a “steppy” cross section of the tube profile once glued together. Then used holesaw and bits of my tube notcher – all clamped to a bedplate at work to machine out the steppy bit into a final 28.6mm tube cross section.
Aluminium slipper block, also with 28.6 diameter. Steel side plates and old washing machine ballraces rolling on top of slipper. Actually needs more leverage than the photo shows (another 1m of steel bar).
Tube is filled with sand. originally kiln dried, but latest batch is my homebrew foundry sand (sand plus bentonite clay). Some cat litter is 100% bentonite clay. Combine with a £10 blender. You can see where this is going….. Blender is now slightly poorly 🙂
Sand held in with 28mm plumbing compression fittings, bored out to 28.6mm. Compression olive just split with a hacksaw to fit on bigger pipe.
Still has a few fine ripples on the back of the tube but generally usable. Not sure if the foundry sand gave any better results for the extra effort.
[/url]
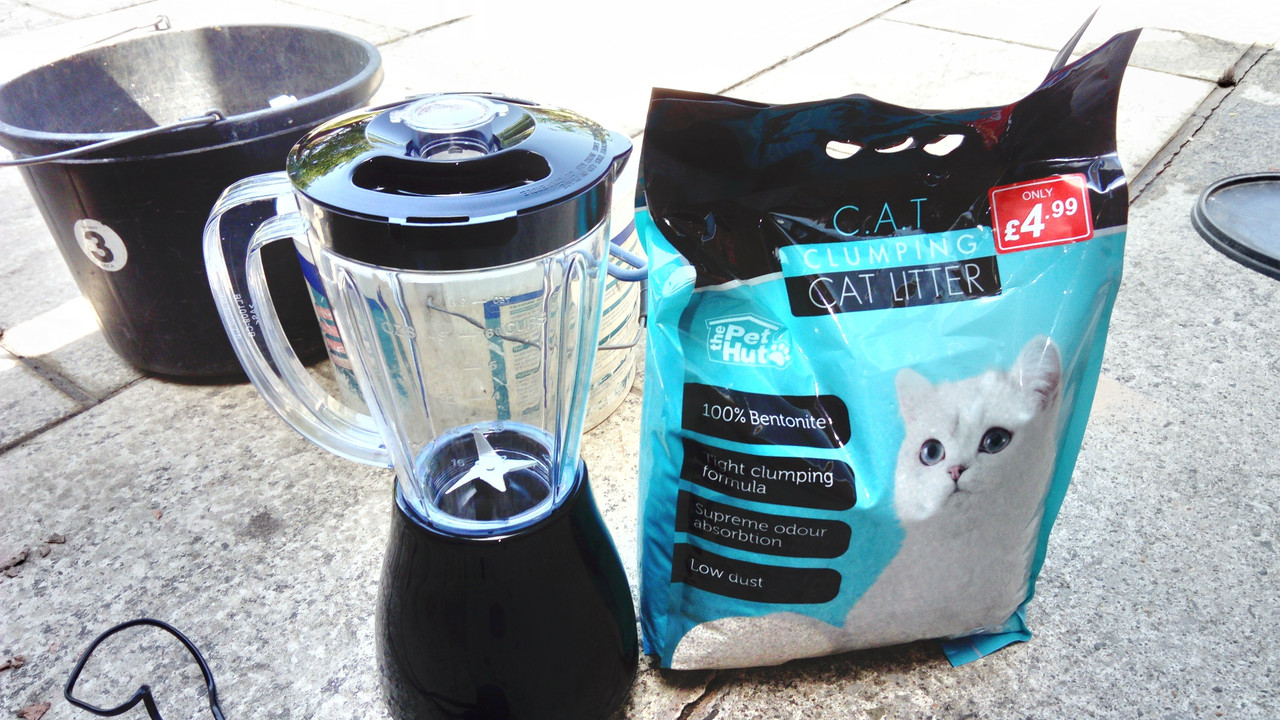
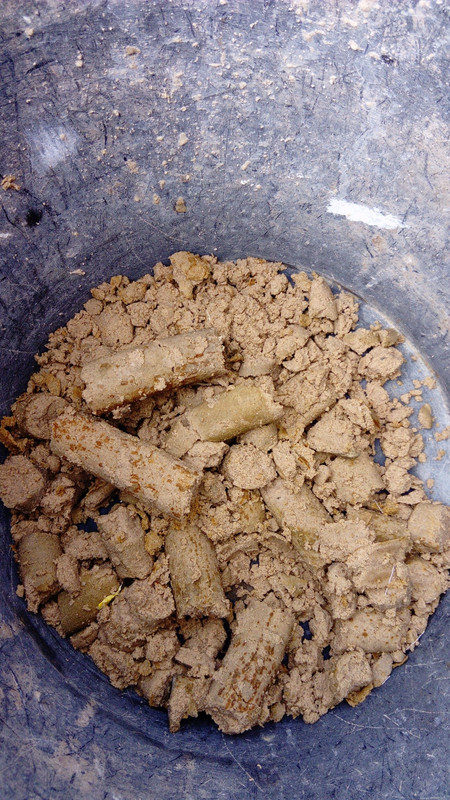