It’s not often that you hear of innovation in materials in the bike industry (beryllium, anyone?). Things seem to have settled down on aluminium, steel, titanium and carbon fibre, with other theoretically better options at present either commercially unviable or, perhaps, undiscovered. Belgian company REIN4RCED (reinforced, geddit?) are aiming to change that with a hybrid carbon fibre and steel weave. So far, their prototypes are showing promise, and they just got investment to build a production line then start manufacturing bike frames and forks in this new material combination.
The thing about conventional carbon fibre parts is that when they break, they break suddenly. By introducing steel fibres into the layup, REIN4RCED are aiming to increase the strength of carbon fibre parts, while also creating parts that give greater warning before they fail if something hits them hard enough that they’re going to. See for yourself in this example:
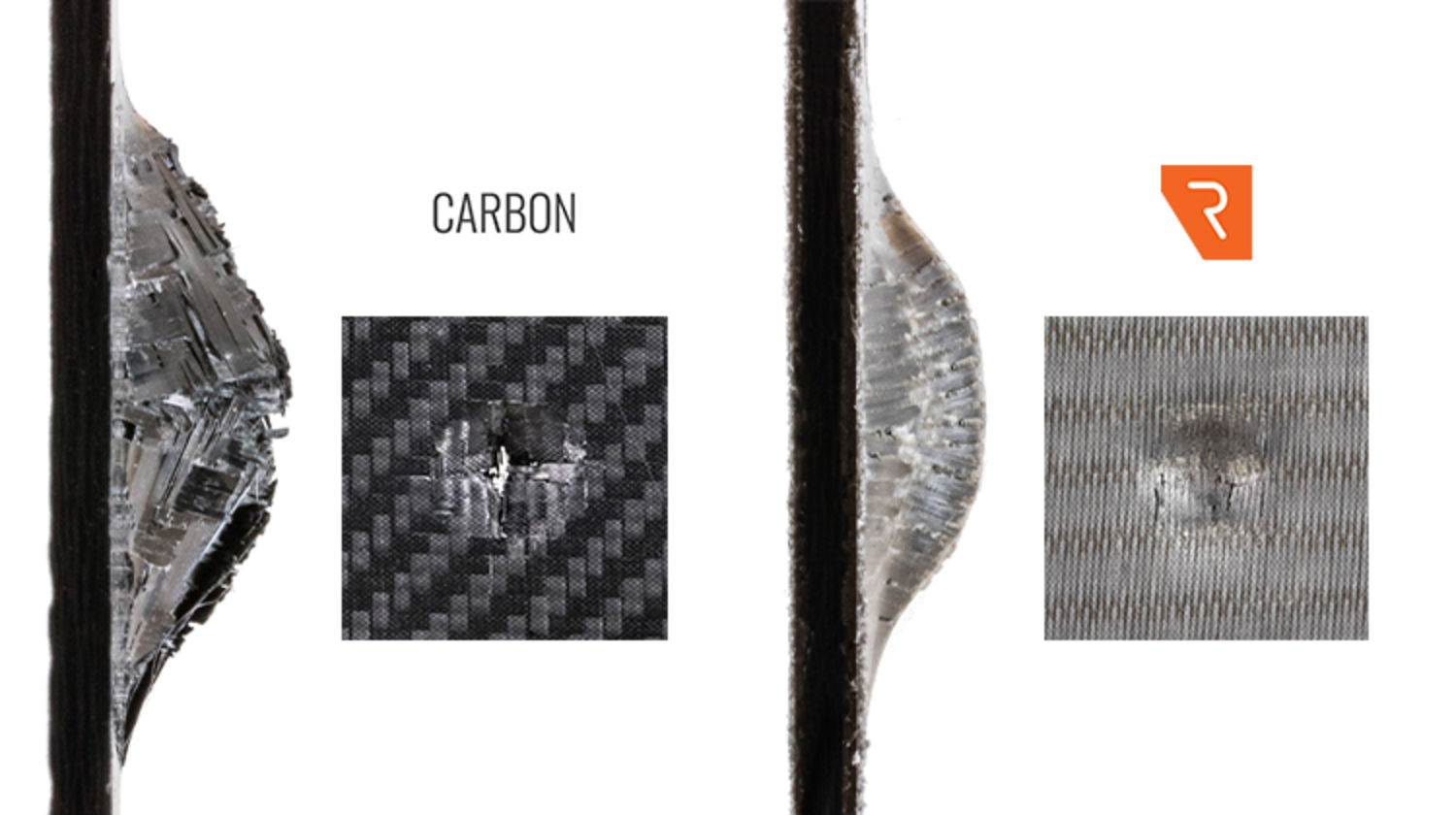
We had a couple of questions beyond the answers on the site, so asked CPO Dave Luyckx.
ST: How does the weight of steel reinforced carbon fibre compare to regular carbon fibre?
DL: “By using a very accurate lay-up and automated process we can achieve comparable or even lower (if really needed) weights. Today, due to the manual labour in Asian manufacturing units, there is a lot of inconsistency and after curing repair work done on each frame. These inconsistencies lower the overall performance and the repair work (mainly esthetic) adds weight without improving the structure.
“Secondly, because of the brittle behavior of carbon composites factories need to factor in a certain margin of error. This is mostly done by increasing the wall thickness or adding high strength fibers to support the high tensile fibers. This again is adding material to increase the impact performance and strength of the final product. They are often optimizing for overall strength of the structure in favor of the athlete’s requirements (weight, stiffness).
“We know that by using the steel fiber and carbon fiber in a very controlled (automated process) environment we can eliminate any excess material described above and we can achieve precise and predictable performance that can compete with the current manually built frames.”
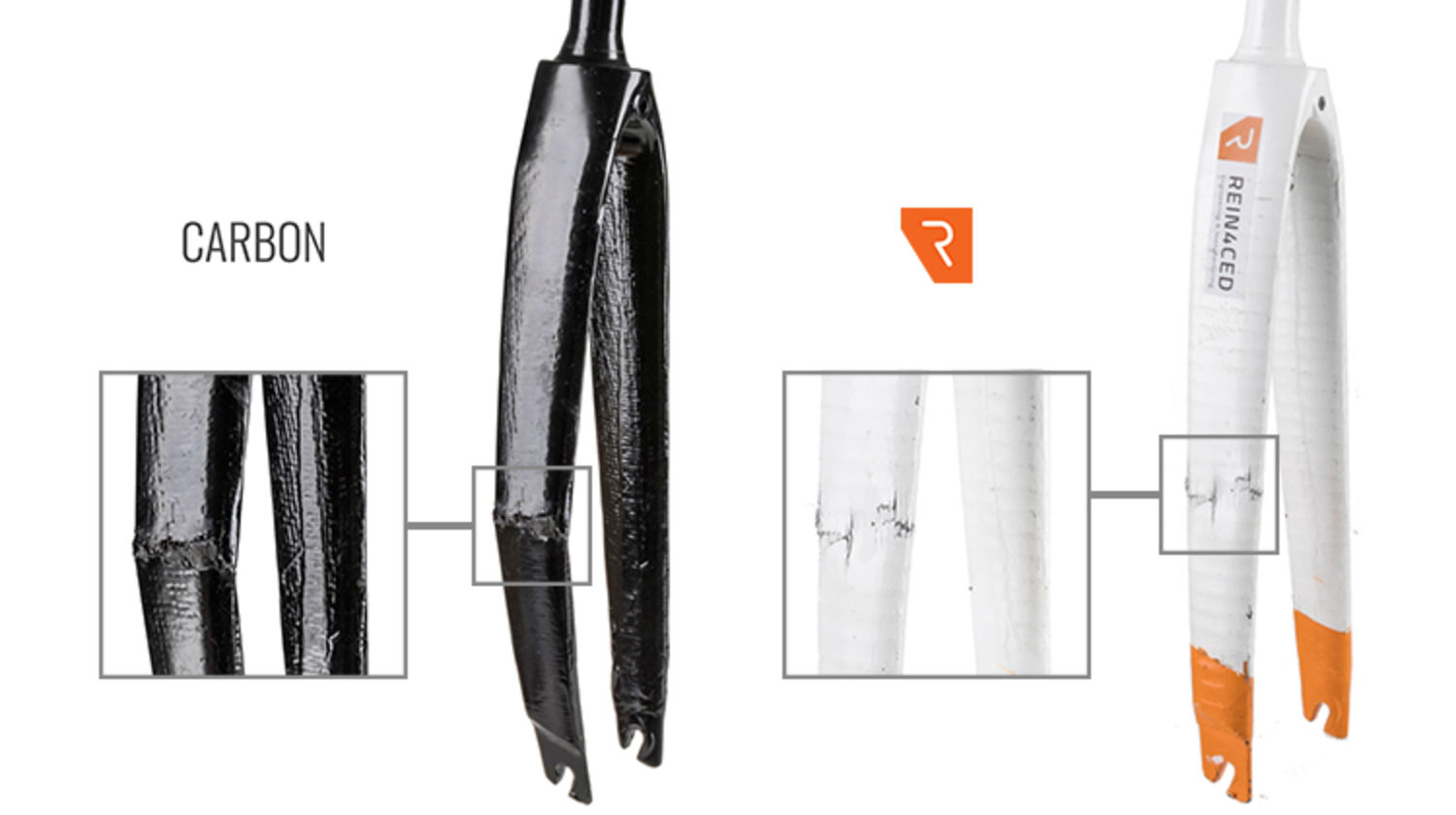
ST: With the damage you show in photos, is Rein4ced’s product designed as a get-home measure? Is the bike still rideable without repairs to the frame?
DL: “We are not claiming that the fork in the picture is not broken. The major difference is that the structure still retains some stiffness and substantial residual stress. The damage in the picture was done by hitting the fork with a force three times higher than was needed to shatter the full carbon fork. The initial impact performance without any damage is many times higher.
“The biggest difference and advantage is that we will never see a sudden catastrophic failure when using our material and you will notice a very distinct “dent” in stead of a full separation of components. The dent is the only practical damage present and it will definitely be possible to ride home without any issues but to exert very high loads after the crash would not be advised and I think the ride home won’t be that smooth anyways if you consider the human damage factor due to a severe crash 😊.
“To give you a prime example:
“If George had used our material he would have sensed something was wrong but he could definitely wait until after the cobblestone section to swap bikes and he could easily finish his race. Now with the sudden collapse he hurt himself badly and his bike was total loss.”
So there we go; it’s certainly an interesting development and seems to have a lot of potential. Claims that the weight can be more consistent and even lower for the same strength make this particularly interesting, perhaps even opening up the way to dingable carbon rims that don’t fail suddenly. What do you think? Will this be a niche, or will all the big brands be unveiling new, reinforced high end frames within a few years?