Take the latest eMTB technology and combine it with an expensive manufacturing process and you’ll build something along the lines of this €16,000 eFanes eMTB.
Bikes built of CNC machined halves are not as uncommon as you might think, and as brands look at building framesets using less traditional methods more CNC wonder bikes are hitting the trails.
Think CNC machined bikes and you will instantly think of Pole’s Machine and Stamina bikes. Not the first CNC machined bikes to hit the dirt, but the first to make CNC’d bikes a viable alternative to traditional welded bikes or moulded carbon frames. In addition to Pole, we’ve seen bikes from Actofive, CNC parts from Hope and even Stanton Bikes is investigating a CNC machined rear end for full suspension bikes.
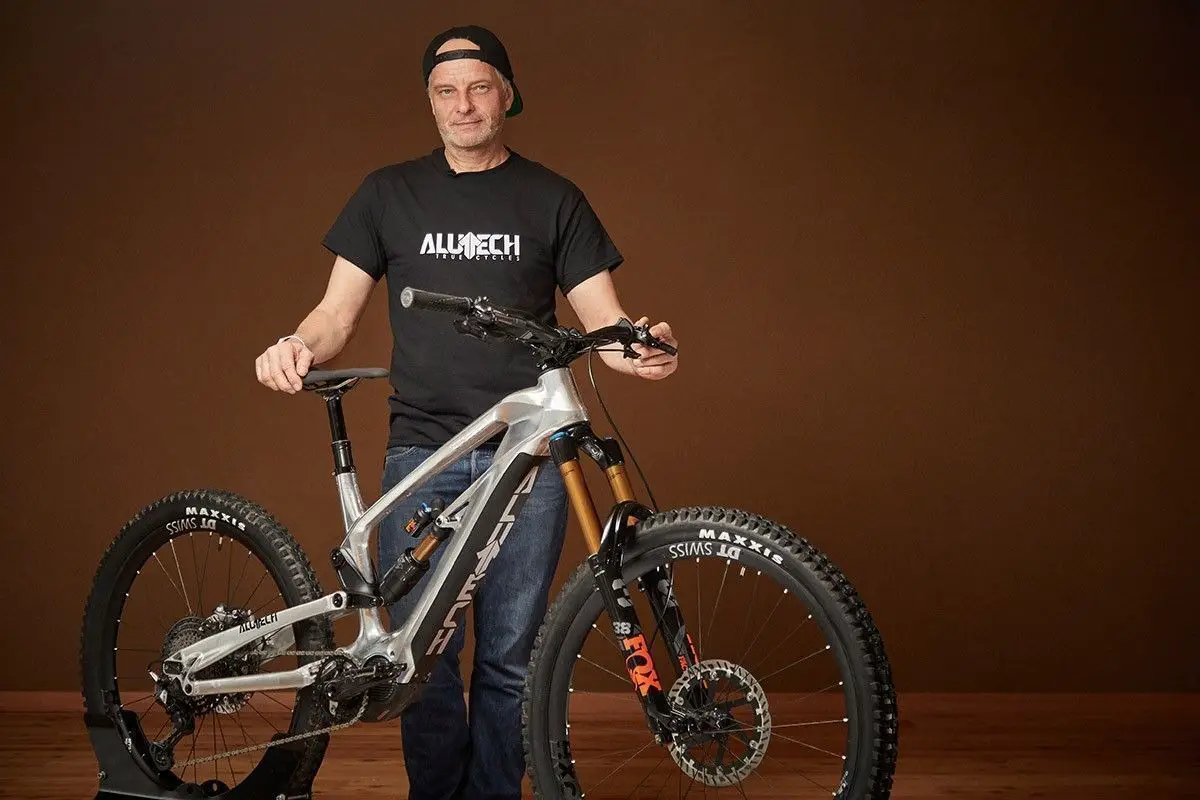
But so far a CNC machined eMTB has been missing from the list of machined bikes, well that is until this week when Alutech revealed that it has made just that. Based on the eFanes eMTB, the CNC eFanes is exactly what you thought it would be a CNC machined eMTB and it’s simply gorgeous.
Whereas Pole has used bolts and bonding processes to fix CNC machined frame halves together, Alutech says they use a welding process. Apparently, the process uses special gases that shield the material and prevent an excess build-up of heat. This lower heat means a lower chance of distortion, which is why Pole and others chose not to weld.
Being a CNC machined frame, Alutech has chosen a mirror-like polished finish to show off the innovative eMTB frame.
What’s most interesting is that the CNC eFanes eMTB isn’t some one-off prototype but a production-ready model that customers can pre-order online today. Due to the complexity of the manufacture, frames will only be offered in size M and L and it doesn’t come cheap! One of these puppies will set you back €15,999!
For the price of a Volkswagen UP GTI you’ll get a mullet eMTB with Fox X2 rear shock, Fox 38 Factory Fork, Shimano XTR drivetrain and Shimano motor and internal battery.
If you fancy one of these for yourself then head on over to the Alutech website and get that credit card boiling.
Comments (9)
Comments Closed
If CNC-ing a frame is that expensive I can’t see it as a viable alternative to the existing frame-building approaches.
If it isn’t intrinsically that costly to do then they’re simply taking the proverbial.
Wonder how many they will sell (or is it just a publicity ploy).
Do they offera crash replacement warranty ?
is that Fred Durst in the pic? Kind of makes me think of what happens when dad’s try to be ‘cool’….
Where’s the EEWINGS & AXS EAGLE FFS
At least the rear end is made properly (cold drawn and welded tubes). CNC is a ludicrous production method for frames.
Not convinced by the idea of CNC an entire frame from a slab. There are tubes going in every direction, so unless they have started from a very fancy forging, they won’t get the best out of the material. If they did start from a forging, then I can see why it might be so expensive for a small run.
It would also need a pile of remanufacturing as they have bearing housings split across the halves.
I used to look after an aerospace component business. If we had a spar with a mount at each end (to hold an engine on a wing for example) we would have two CNC fittings welded to a strut. Not make the whole thing in two pieces and weld down the axis across a bearing mount.
I imagine the raw materials must be expensive too. I assume it isn’t just bog standard aluminium. The frame looks about 4 inches wide from the photo of where the battery attaches so this would be two two-inch slabs of aluminium the size of the front triangle.
I suppose that they might have just done it to see if they could and once they had all that worked out, it would be simple enough to reproduce so why not make some more. If their starting point was as a commercial exercise, that would seem a little optimistic.
It is very pretty though.
Couple of comments:
CNC from billet is a really, really stupid, wasteful and not terribly strong way of making a bike frame. It has a small amount of use to prototype basic geo, but that’s it.
And that’s not got a “polished mirror” finish, because you can still see the tool path, persumably deliberately left in place so you can brag to your mates about how stupid your frame is
And thirdly “Alutech says they use a welding process. Apparently, the process uses special gases that shield the material and prevent an excess build-up of heat” is just welding.
Pretty much all welding uses gases to do exactly that (the exception being low temperature welding, like friction stir welding (which is what they should be using to join the halves), and huge industrial processes that use a dry inert barrier, often using sand/silica
All that effort just end up with a frame that looks like loads of others. At least Poles stands out from the crowd